|
|
|
КАРТА
САЙТА
|
ДОПОЛНИТЕЛЬНАЯ
ПОЛНОТЕКСТОВАЯ ИНФОРМАЦИЯ
УЧЕБНО-ПРАКТИЧЕСКОГО
НАЗНАЧЕНИЯ :
|
|
|
|
|
|
|
|
|
|
|
|
|
|
|
Дополнительные
источники
по теме :
|
|
|
|
Зорин,
Н. Е. Материаловедение сварки. Сварка плавлением [Текст]
: учебное пособие / Н. Е. Зорин, Е. Е. Зорин. – 2-е изд.,
стер. – СПб. : Лань, 2017. – 164 с. : ил. – (Учебники
для вузов. Специальная литература).
(полное
содержание см. здесь...) |
|
|
|
|
|
Быковский,
О. Г. Сварочное дело [Текст] : учебное пособие для учреждений
СПО / О. Г. Быковский. – М. : Кнорус, 2017. – 272 с. :
ил., табл. – (Среднее профессиональное образование).
(полное
содержание см. здесь...)
|
|
|
|
|
|
Маслов,
Валентин Иванович. Сварочные работы : [Текст] учебник
: для использования в учебном процессе образовательных
учреждений, реализующих программы начального профессионального
образования по профессии "Сварщик" / В. И. Маслов.
- 14-е изд., стер. - Москва : Академия, 2018. - 282 с.
: ил., табл. - (Профессиональное образование). |
|
Аннотация:
Содержание учебника базируется на программных материалах
по химии, физике, технологии металлов и конструкционных
материалов, электронике и другим техническим предметам.
Книга содержит общие сведения о сварке, сварных соединениях
и швах, электрической сварке плавлением, газовой сварке
и резке, контроле качества сварных швов. Кроме основных
видов сварки рассмотрены их разновидности. |
|
|
|
Михайлицын,
С. В. Сварка специальных сталей и сплавов [Текст] : учебное
пособие / С. В. Михайлицын, М. А. Шекшеев, А. И. Беляев.
– Магнитогорск : МГТУ им. Г. И. Носова, 2015. – 204 с. |
|
|
|
Овчинников,
Виктор Васильевич. Дефектация сварных швов и контроль
качества сварных соединений [Текст] : учебник : [для общеобразовательных
учреждений реализующих программы НПО] / В. В. Овчинников.
- 4-е изд.. стер. - Москва : Академия, 2018. - 223, [1]
с. : ил. - (Профессиональное образование. Профессиональный
модуль). |
|
Аннотация
: Учебник
создан в соответствии с Федеральным государственным образовательным
стандартом среднего профессионального образования но специальности
«Сварочное производство», ПМ.03 «Контроль качества сварочных
работ». Рассмотрены типичные дефекты сварных соединений,
их влияние на работоспособность сварных конструкций. Описана
международная кодировка дефектов в зависимости от их вида
и места расположения в сварном соединении. Изложены широко
применяемые в промышленности разрушающие и неразрушающие
методы обнаружения и идентификации дефектов (внутренних
и наружных). Представлены методы определения остаточных
напряжений в конструкциях. Приведены рациональные методы
устранения дефектов сварки плавлением, электронно-лучевой
и контактной сварки. Для студентов учреждений среднего
профессионального образования. |
|
|
|
|
|
|
Овчинников,
Виктор Васильевич. Ручная дуговая сварка (наплавка, резка)
плавящимся покрытым электродом [Текст] : учебник : [для
использования в образовательном процессе образовательных
организаций, реализующих программы среднего профессионального
образования по профессии "Сварщик [ручной и частично
механизированной сварки (наплавки)] / В. В. Овчинников..
- 2-е изд., стер. - Москва : Академия, 2018. - 206 с.
: ил. |
|
Аннотация:
Учебник содержит сведения по материалам,
свариваемым ручной дуговой сваркой покрытым электродом,
конструкции покрытых электродов, маркам электродов, принципам
выбора марки электрода для сварки конкретного металла.
Приведены данные по технике выполнения швов в различных
пространственных положениях плавящимся покрытым электродом,
по технологии выполнения наплавки и резки. Рассмотрены
особенности дуговой сварки и наплавки неплавящимся электродом
в защитном газе, приведены марки неплавящихся электродов,
присадочной проволоки и защитных газов, вопросы технологии
дуговой сварки и наплавки неплавящимся электродом в защитном
газе различных металлов и сплавов. Соответствует ФГОС
СПО последнего поколения. Рекомендовано для освоения профессий
из списка ТОП-50 наиболее востребованных на рынке труда,
новых и перспективных профессий. Для студентов, обучающихся
по специальности «Сварщик (ручной и частично механизированной
сварки (наплавки)». |
|
|
|
|
|
Овчинников,
В. В. Сварка и резка деталей из различных сталей, цветных
металлов и их сплавов, чугунов во всех пространственных
положениях [Текст] / В. В. Овчинников. – 3-e изд., стер.
– М. : Академия, 2017. – 300 с. |
|
|
|
Паршин,
С. Г. Технология сварки. Сварка плавлением. Технология
сварки углеродистых, низколегированных сталей и чугунов
[Текст] : учебное пособие / С. Г. Паршин. – СПб. : Изд-во
Политехн. ун-та, 2015. – 154 с. |
|
|
|
Синяков,
Кирилл Александрович. Сварка специальных сталей [Текст]
: учебное пособие / К. А. Синяков ; Министерство образования
и науки Российской Федерации, Санкт-Петербургский политехнический
университет Петра Великого. - Санкт-Петербург : Изд-во
Политехнического ун-та, 2018. - 153 с. : ил., табл. |
|
Аннотация: В
пособии приведены основные сведения о влиянии легирующих
элементов на процессы, происходящие при сварке, условия
кристаллизации металла сварочной ванны, механизмы химической
и физической неоднородности, свариваемость, структуру
и специальные свойства основных групп сталей. Пособие
содержит информацию о возможных дефектах и способах их
предупреждения и устранения. Предназначено для студентов
вузов, обучающихся по сварочным специальностям и специальностям,
связанным с ремонтом и восстановлением деталей машин и
аппаратов. |
|
|
|
|
Отличие
техники сварки высоколегированных сталей и сплавов от техники
сварки обычных низколегированных сталей заключается в уменьшении
вылета электрода примерно
в 1,5–2,0 раза ввиду повышенного электросопротивления сварочных
проволок, применяемых для сварки высоколегированных сталей и сплавов.
Сварку ведут на постоянном токе. Высоколегированные стали и сплавы
рекомендуется сваривать швами небольшого сечения. Это предопределяет
использование сварочной проволоки диаметром 2–3 мм.
При сварке аустенитных сталей величину
тока следует уменьшить на 10–30 %, так как их температура плавления
на 50...150 °С ниже, чем у обычных углеродистых сталей.
При сварке под флюсом используют
проволоки, предназначенные для сварки высоколегированных сталей
и сплавов и выпускаемые в соответствии с государственными стандартами
и ведомственными техническими условиями.
Сварку
ведут под флюсами типа АНФ-5, АНФ-8, АНФ-14, АНФ-16, АНФ-17, АНФ-22,
АНФ-23, АНФ-24, 48-ОФ-6, АН-10, АН-17, АН-18, АН-22, АН-26, АН-30
и др.
Дуговую сварку в защитных
газах можно осуществлять в среде инертных (аргон, гелий) и активных
(углекислый газ) газов, а также в различных смесях инертных
или активных газов и инертных с активными. Этот способ сварки
можно использовать для соединения металлов широкого диапазона
толщин – от десятых долей до десятков миллиметров.
При сварке плавящимся электродом
появляется возможность изменения характера металлургического воздействия
за счет значительного изменения состава защитной атмосферы, например
создания окислительных условий в дуге путем применения смеси газов,
содержащих кислород, углекислый газ и др. Этим способом можно
выполнять сварку в различных пространственных положениях, что
делает ее целесообразной в монтажных условиях по сравнению с ручной
дуговой сваркой покрытыми электродами. Сварку в защитных газах
можно выполнять неплавящимся вольфрамовым или плавящимся электродом.
Вольфрамовым электродом
сваривают в инертных газах или их смесях. Для сварки
высоколегированных сталей и сплавов используют аргон. Обычно сварку
вольфрамовым электродом технически и экономически целесообразно
использовать при сварке для металлов толщиной до 7 мм (при толщине
до 1,5 мм применение других способов дуговой сварки практически
невозможно из-за образования прожогов). Однако в некоторых случаях,
например при сварке неповоротных стыков труб, сварку вольфрамовым
электродом применяют на сталях и больших толщин.
Высокое качество формирования обратного
валика вызываст необходимость применения этого способа и при сварке
корневых швов в разделках при изготовлении ответственных толстостенных
изделий. В зависимости от толщины стали и конструкции сварного
соединения сварку выполняют с присадочным материалом или без него
вручную с использованием специальных горелок или автоматически.
Сварку ведут на постоянном токе прямой полярности. Исключение
составляют стали и сплавы с повышенным содержанием алюминия, когда
для разрушения поверхностной пленки оксидов, богатой алюминием,
следует применять переменный ток.
Сварку можно выполнять непрерывно
горящей или импульсной дугой. Импульсная дуга благодаря особенностям
ее теплового воздействия позволяет уменьшить протяженность ЗТВ
и коробление свариваемых кромок, а также сваривать металл малой
толщины при хорошем формировании шва.
Для улучшения формирования корня
шва используют поддув газа, а при сварке корневых швов на металле
повышенных толщин – специальные расплавляющиеся вставки.
Сварку плавящимся электродом выполняют
в инертных, активных газах или их смесях. При сварке высоколегированных
сталей и сплавов, содержащих легкоокисляющиеся элементы (алюминий,
титан и др.), следует использовать инертные газы, преимущественно
аргон.
При сварке в инертных газах возможен
капельный и струйный перенос электродного металла. При струйном
переносе дуга имеет наиболее высокую стабильность и значительно
улучшается перенос электродного металла в сварочную ванну; практически
исключается разбрызгивание металла. Это особенно важно при сварке
швов в вертикальном и потолочном положениях.
Отсутствие разбрызгивания и связанных
с этим очагов коррозии благоприятно при сварке коррозионно-стойких
и жаростойких сталей. Однако струйный перенос возможен на токах
выше критических, при которых возможно образование прожогов при
сварке тонколистового металла. Добавка в аргон до 3–5 % кислорода
уменьшает величину критического тока. Кроме того, создание при
этом окислительной атмосферы в зоне дуги уменьшает и вероятность
образования пор, вызванных водородом. Последнее достигается и
применением смеси аргона с 15–20 % углекислого газа. Это позволяет
уменьшить и расход дорогого и дефинитного аргона. Однако при указанных
добавках газон увеличивается угар легирующих элементов, а при
добавке углекислого газа возможно и науглероживание металла шва.
Добавкой к аргону 5–10 % азота может быть повышено его содержание
в металле шва. Азот, являясь сильным аустенитизатором, позволяет
изменять структуру металла шва.
При сварке в углекислом газе происходят
значительное разбрызгивание металла (потери достигают 10–12 %)
и образование на поверхности шва плотных пленок оксидов, снижающих
коррозионную стойкость и жаростойкость сварного соединения.
Для снижения разбрызгивания при
сварке в углекислом газе применяют импульсную сварку. Наличие
на поверхности швов трудноудаляемой пленки оксидов делает практически
невозможной сварку в углекислом газе многослойных швов.
Сварку плавящимся электродом в защитных
газах выполняют полуавтоматически или автоматически на постоянном
токе обратной полярности.
Сварку плавящимся электродом выполняют
проволоками, предназначенными для сварки высоколегированных сталей
и сплавов. При сварке в углекислом газе аустенитных и хромистых
сталей целесообразно применять проволоки с повышенным содержанием
хрома и с дополнительным легированием кремнием, ниобием, титаном,
алюминием.
Для высоколегированных сталей и
сплавов начинает применяться и плазменно-дуговая сварка. Большое
преимущество – малый расход защитного газа. Получение плазменных
струй различного сечения (круглого, прямоугольного и т.д.) и значительное
изменение расстояния от плазменной горелки до изделия значительно
расширяют технологические возможности этого способа. Плазменно-дуговую
сварку можно использовать для весьма тонких металлов и для металла
толщиной до 12 мм. Применение ее для соединения сталей большой
толщины затрудняется возможностью образования в швах подрезов.
Для электрошлаковой сварки используют
в основном фторидные флюсы типа АНФ-6, АНФ-8, АНФ-14, АНФ-26 и
др., а также чистый CaF2 без добавок. Применение для электрошлаковой
сварки даже фторидных безокислительных флюсов не всегда гарантирует
хорошее усвоение сварочной ванной элементов, обладающих большим
сродством к кислороду, поэтому в ряде случаев приходится защищать
шлаковую ванну инертным газом (аргоном).
Применяют проволоку, предназначенную для сварки высоколегированных
сталей и сплавов. Электрошлаковую сварку можно выполнять проволочным
или пластинчатым электродами. Изделия большой толщины со швами
небольшой протяженности целесообразнее сваривать пластинчатым
электродом.
Изготовление пластинчатого электрода
более простое. Однако сварка проволокой позволяет в более широких
пределах, варьируя режим, изменять форму металлической ванны и
характер кристаллизации металла шва, а это один из действенных
факторов, обеспечивающих получение швов, свободных от горячих
трещин. В то же время жесткость сварочной проволоки затрудняет
длительную и надежную работу токоподводящих и подающих узлов сварочной
аппаратуры.
Электронно-лучевая сварка
обеспечивает возможность за один проход сварить без разделки кромок
металл большой толщины с минимальной протяженностью ЗТВ и очень
малым коэффициентом формы шва, что является важным технологическим
преимуществом этого способа. Однако и при этом способе возможно
образование в шве и ОШЗ горячих трещин и локальных разрушений
в ЗТВ. Электронно-лучевая сварка в вакууме облегчает удаление
примесей и газов, но увеличивает испарение легирующих элементов.
При глубоком и узком проваре часть газов может задержаться растущими
кристаллами в шве и образовать поры. Сварка материала большой
толщины затруднена из-за непостоянства глубины проплавления. Сложность
аппаратуры и процесса обусловливает применение электронно-лучевой
сварки в основном при изготовлении ответственных конструкций из
жаропрочных сталей и сплавов.
Сварку металла толщиной до 1 мм
выполняют расфокусированным пучком электронов, а при большой толщине
рекомендуют остро-фокусированный пучок. Для расширения технологических
возможностей сварки целесообразно сообщить колебания электронному
лучу поперек стыка, вдоль стыка или перемещать его по окружности,
что улучшает структуру и свойства металла шва. Применение электроннолучевой
сварки позволяет повысить стойкость швов против образования горячих
трещин. Сварку выполняют в диапазоне средних скоростей при наибольшей
удельной мощности луча. |
 |
|
|
|
|
ПОЛНОТЕКСТОВАЯ
ИНФОРМАЦИЯ
УЧЕБНО-ПРАКТИЧЕСКОГО
НАЗНАЧЕНИЯ
|
Черепахин,
А. А. Технология сварки сталей [Электронный ресурс] / А. А.
Черепахин // Основы сварочного производства и теория сварочных
процессов : учебное пособие / А. А. Черепахин ; под ред. Л. П.
Андреева [и др.]. – М. : Кнорус, 2020. – С. 361-364.
|
|
|
Низкоуглеродистые
конструкционные стали |
В
сварочной технике углеродистые стали подразделяют на три группы:
низкоуглеродистые, среднеуглеродистые и высокоуглеродистые.
Для сварных конструкций в подавляющем большинстве используют
низкоуглеродистые стали, редко – среднеуглеродистые стали и
практически не используют высокоуглеродистые стали.
К низкоуглеродистым относятся
стали с содержанием углерода до 0,25 %. По качественному признаку
эти стали разделяют на две группы: обыкновенного качества (стали
марок Ст1, Ст2, Ст3 и др.) и качественные (стали марок Ст10,
15, 20 др.).
Стали этой группы относятся к
разряду хорошо сваривающихся практически всеми видами сварки
металлов.
Основными требованиями
при их сварке являются следующие:
-
обеспечение равнопрочности сварного соединения основному металлу;
-
отсутствие дефектов (типы трещин, непроваров, пор, подрезов
и других дефектов);
-
стойкость сварного соединения против перехода в хрупкое состояние;
-
требуемая форма сварного шва и соединения.
В
некоторых случаях дополнительно вводятся требования высокой
коррозионной стойкости сварных соединений, их работоспособности
в условиях вибрационных и ударных нагрузок, повышенных или пониженных
температур и другие специальные свойства.
Механические свойства
металла шва и сварного соединения зависят от его структуры,
которая определяется химическим составом, режимом сварки и предыдущей
и последующей термической обработкой.
Химический состав металла шва зависит от доли участия основного
и электродного металла в образовании шва и взаимодействий между
металлом и шлаком и металлом и газовой фазой.
При сварке низкоуглеродистых сталей
металл шва незначительно отличается по составу от основного
металла. Это отличие в основном сводится к снижению в металле
шва углерода для предупреждения образования структур закалочного
характера при повышенных скоростях охлаждения, так как металл
электродного стержня или электродной проволоки содержит меньше
углерода, чем основной металл, и повышению содержания марганца
и кремния.
Возможное снижение прочности металла
шва, вызванное уменьшением содержания углерода, компенсируется
за счет увеличения скорости его остывания и легирования металла
через проволоку, покрытие или флюс марганцем и кремнием.
Повышенные скорости
охлаждения металла шва способствуют увеличению его прочности,
однако при этом снижаются пластические свойства (относительное
удлинение, относительное сужение) и ударная вязкость. Это объясняется
изменением количества и строения перлитной фазы. Скорость охлаждения
металла шва определяется толщиной свариваемого металла, конструкцией
сварного соединения, режимом сварки и начальной температурой
изделия.
Пластическая деформация, возникающая
в металле шва под действием сварочных напряжений, также повышает
предел текучести металла шва.
Свойства сварного соединения зависят
не только от свойств металла шва, но и от свойств основного
металла в зоне термического влияния (ЗТВ).
Структура, а значит, и свойства
основного металла в ЗТВ зависят от его химического состава и
изменяются в зависимости от термического цикла сварки.
Решающими факторами термического
цикла сварки являются максимальная температура, достигаемая
металлом в рассматриваемом объекте, и скорость его охлаждения.
Ширина и конечная структура различных
участков ЗТВ определяются способом и режимом сварки, составом
и толщиной основного металла.
Конструкции из низкоуглеродистых
сталей в некоторых случаях подвергаются термической обработке
(ТО) после сварки. Задача ТО обычно сводится к снятию сварочных
напряжений (для этого применяют высокий отпуск) или к выравниванию
свойств и улучшению структуры отдельных участков сварного соединения
(для этого применяют нормализацию – нагрев до температуры 920...940
°С, остывание на воздухе с последующим высоким отпуском). Применяют
также и более сложные виды термической обработки (например,
закалку с последующим отпуском) с целью снятия структурных напряжений
и повышения механических свойств металла шва.
Швы,
сваренные на низкоуглеродистых сталях всеми методами и способами
сварки плавлением, обладают удовлетворительной стойкостью против
образования кристаллизационных трещин, что обусловлено низким
содержанием в основном металле и, следовательно, в металле шва
углерода. Однако при сварке низкоуглеродистой стали, содержащей
углерод по верхнему пределу (0,21–0,25 %) возможно образование
кристаллизационных трещин.
На практике низкоуглеродистые
стали сваривают ручной дуговой сваркой, порошковой проволокой,
дуговой сваркой под флюсом и в защитных газах, электрошлаковой
сваркой и газовой сваркой.
Конструктивные элементы
подготовки кромок и размеры сварных швов выбирают в соответствии
с ГОСТ 5264–80 «Ручная дуговая сварка. Соединения сварные. Основные
типы, конструктивные элементы и размеры», ГОСТ 8713–79 «Сварка
под флюсом. Соединения сварные. Основные типы, конструктивные
элементы и размеры», ГОСТ 14771–76 «Дуговая сварка в защитных
газах. Соединения сварные. Основные типы, конструктивные элементы
и размеры», ГОСТ 15164–78 «Электрошлаковая сварка. Соединения
сварные. Основные типы, конструктивные элементы и размеры»,
а также в соответствии с отраслевыми техническими условиями.
Сварку ведут присадочными материалами
с более низким значением углерода, но с более высоким значением
кремния и марганца в электроде или в покрытии (флюсе).
При ручной дуговой сварке чаше
всего применяют электроды типа Э38, Э42, Э42А, Э46, с кислым
(электроды марок СМ-5. ЦМ-7 и др.), рутиловым (электроды марок
МР-1, МР-3, АНО-1, АНО-3, АНО-4, АНО-5, АНО-6, ОЗС-3, ОЗС-4,
ОЗС-6 и др.), целлюлозным (электроды марок BCЦ-1, ВСЦ-2, BCЦ-4
и др.), основным (электроды марки УОНИ-13/45 и др.) и другими
покрытиями.
Ручную дуговую сварку
используют для получения однослойных и многослойных стыковых
(односторонних и двусторонних) и угловых швов в различных пространственных
положениях без разделки кромок и с разделкой кромок.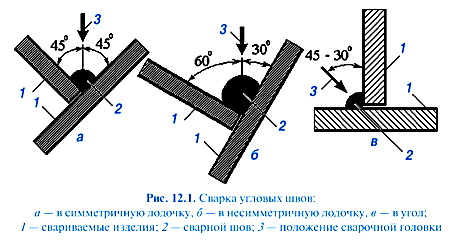
Для сварки под флюсом применяют
плавленые флюсы типа АН-348-А, OCЦ-45 (высококремнистые высокомарганцовистые
оксидные флюсы) или керамические флюсы типа К-10, К-11 (их шлаковая
основа близка к шихте флюсов ОСЦ-45, АН-348-А) и проволоки Св-08,
Св-08А, Св-08ГА. Керамические флюсы наиболее рационально и экономически
оправданно использовать для сварки ржавого и увлажненного металла,
когда операция зачистки, обеспечивающая полное удаление ржавчины,
вызывает значительные трудности.
Автоматическую сварку выполняют
электродной проволокой диаметром 3–5 мм, полуавтоматическую
– проволокой диаметром 1,2–2 мм.
Сварку под флюсом применяют для
получения стыковых и угловых швов на постоянном токе обратной
полярности или переменном токе.
С помощью сварки под флюсом получают
односторонние и двусторонние, однослойные и многослойные стыковые
швы с разделкой и без разделки кромок. Сварку осуществляют на
флюсовой подушке, на медной подкладке, с ручной подваркой.
Сварка угловых швов под флюсом осуществляется
при положении «в лодочку» и «в угол» (рис. 12.1). Угловые швы
выполняют однослойными и многослойными, без разделки кромок
и с разделкой кромок.
При
сварке в защитных газах чаше всего используют углекислый газ,
а также смеси углекислого газа с аргоном или кислородом до 30
% кислорода.
Кислород уменьшает разбрызгивание
расплавленного металла, повышает его жидкотекучесть, а также
связывает водород и уменьшает его влияние на образование пор.
Добавки аргона изменяют глубину проплавления, форму шва, стабильность
дуги и позволяют регулировать концентрацию легирующих элементов
в металле шва. Аргон и гелий в качестве защитных газов применяют
только при сварке конструкции ответственного назначения плавящимся
или неплавящимся вольфрамовым электродом.
Сварку в атмосфере инертных газов
вольфрамовым электродом применяют для металла толщиной до 2
мм. Сварку выполняют на постоянном токе (как правило, прямой
полярности) или на переменном токе.
Сварку плавящимся электродом в атмосфере инертных газов применяют
для металла толщиной более 0,8 мм. Диаметр электродной проволоки
выбирают в зависимости от толщины свариваемого металла в пределах
0,5–3,0 мм. Сварку выполняют на постоянном токе обратной полярности.
Сварку в углекислом газе выполняют
плавящимся электродом (для толщин свыше 0,8 мм) или неплавящимся
угольным (графитовым) электродом (для толщин до 2 мм).
При автоматической и полуавтоматической
сварке плавящимся электродом швов, расположенных в различных
пространственных положениях, обычно используют электродную проволоку
диаметром до 1,2 мм; при сварке в нижнем положении – диаметром
1,2–3,0 мм. Сварку выполняют на постоянном токе обратной полярности.
На свойства металла шва значительное
влияние оказывает качество углекислого газа. При повышенном
содержании азота и водорода, а также влаги в швах могут образовываться
поры. Сварка в углекислом газе менее чувствительна к отрицательному
влиянию ржавчины.
Сварку в защитных газах используют
для получения однослойных и многослойных стыковых (односторонних
и двусторонних) и угловых швов в различных пространственных
положениях без разделки кромок, с отбортовкой кромок и с разделкой
кромок.
В качестве присадочного материала
или электродной проволоки применяют проволоки Св-08ГС, Св-08Г2С,
Св-12ГС.
Для сварки открытой дугой применяют
порошковые проволоки рутилоорганического типа (марок ПП-AH1,
ПП-1ДСК и др.) и карбонатно-флюоритного тина (марок ПП-АН2,
ПП-АН3, ПП-АН6 и др.).
Сварку порошковой проволокой рутилорганического
типа, как правило, выполняют на постоянном токе обратной полярности,
а сварку порошковой проволокой карбонатно-флюоритного типа –
на постоянном токе прямой полярности.
Сварку порошковой проволокой,
как правило, выполняют на постоянном токе и используют для получения
стыковых и угловых швов в основном в нижнем и вертикальном положениях.
При электрошлаковой сварке применяют
проволоки Св-10Г2, Св-12Г2, Св-08ГС, Св-08ГА, Св-08А и флюсы
типа АН-8, АН-22 (низкокремнистые марганцовистые), типа АНФ-8
(фторидные), типа ФЦ-7 (высококремнистые среднемарганцовистые
оксидные) и типа АН-348-А.
Сварку осуществляют проволочным
электродом, пластинчатым электродом и плавящимся мундштуком.
Состав пластинчатого электрода и плавящегося мундштука аналогичен
составу применяемых проволок.
Газовую сварку осуществляют нормальным ацетилено-кислородным
пламенем с использованием проволок Св-08 и Св-08А.
При сварке металла толщиной до
3 мм используют левый способ сварки, расход ацетилена 100–200
л/ч на 1 мм толщины. Для более толстого металла применяют правый
способ сварки, который для данных толщин более производителен,
расход ацетилена 120–150 л/ч на 1 мм толщины.
|
Среднеуглеродистые
конструкционные стали |
К
среднеуглеродистым конструкционным сталям по классификации, принятой
в сварочной технике, относятся стали, содержащие 0,26–0,45 % углерода.
В эту группу входят стали 25, 30, 35, 40 и др. К этой же группе
относятся стали 25Г, 30Г и 35Г с повышенным содержанием марганца.
На сталях этой группы можно получать удовлетворительное соединение
всеми видами сварки.
Среднеуглеродистые стали находят
применение в судостроении, машиностроении и других отраслях промышленности.
Для сварнолитых и сварнокованых конструкций находят применение
преимущественно стали 35 и 40.
Технология сварки среднеуглеродистых
сталей строится на той же основе, что и технология сварки низкоуглеродистых
сталей. Однако повышенное содержание углерода в сравнении с низкоуглеродистыми
сталями предопределяет трудности сварки этих сталей. К ним относятся
низкая стойкость металла шва против кристаллизационных трещин,
возможность образования малопластичных закалочных структур и трещин
в ЗТВ и трудность обеспечения равнопрочности металла шва с основным
металлом.
Для преодоления этих трудностей
и в первую очередь для повышения стойкости металла шва против
кристаллизационных трещин при всех видах сварки плавлением стремятся
снизить содержание углерода в металле шва.
Это обычно достигается за счет применения
электродных стержней и электродной проволоки с пониженным содержанием
углерода и уменьшения доли основного металла в металле шва. Стремятся
также обеспечить получение швов с большим значением коэффициента
формы и применяют предварительный и сопутствующий подогрев, двухдуговую
сварку и раздельные ванны и модифицирование металла шва.
Для сварки среднеуглеродистых сталей
чаше всего применяют предварительный подогрев до температуры 250...300
°С, позволяющий повысить на 0,01–0,02 % допустимое содержание
углерода в металле шва, при котором еще не образуются трещины,
и предупредить образование закалочных структур в ЗТВ. Следует
отметить, что чрезмерный подогрев может вызвать образование трещин
вследствие увеличения провара основного металла и связанного с
этим повышения содержания углерода в металле шва.
Для снижения доли основного металла
в шве дуговую сварку среднеуглеродистых сталей, как правило, ведут
с разделкой кромок на режимах, обеспечивающих минимальное проплавление
основного металла и максимальное значение коэффициента формы шва.
В результате этого происходит снижение углерода в металле шва
и, следовательно, повышение стойкости металла шва против кристаллизационных
трещин.
Для повышения доли электродного
металла в металле шва принимают также меры по увеличению коэффициента
наплавки. В частности, при механизированных способах сварки это
достигается применением сварочной проволоки малого диаметра (2–3
мм) и минимального сварочного тока. Лучшие результаты получаются
при постоянном токе прямой полярности. Необходимо отметить, что
сварку пол флюсом среднеуглеродистых сталей ведут па режимах,
не характерных для этого высокопроизводительного способа, поэтому
он не получил широкого применения при изготовлении конструкций
из среднеуглеродистых сталей.
Эффективным и надежным средством
достижения равнопрочности металла шва при низком содержании в
нем углерода служит дополнительное легирование элементами, упрочняющими
феррит, например марганцем и кремнием.
Чтобы избежать образования малопластичных
и хрупких закалочных структур в ЗТВ, при сварке среднеуглеродистых
сталей следует замедлять остывание изделий путем снижения скорости
сварки, предварительного подогрева металла, сварки двумя и более
раздвинутыми дугами.
Чем больше содержание углерода в
стали, тем выше должна быть температура подогрева металла при
сварке.
Однако даже при использовании всех
указанных приемов сварные соединения на среднеуглеродистой стали
чаше всего получаются недостаточно пластичными, так как закалка
основного металла в ЗТВ полностью не предотвращается. Если к сварному
соединению предъявляются требования высокой пластичности, то для
выравнивания свойств приходится применять последующую термическую
обработку, чаще всего закалку с отпуском.
На практике среднеуглеродистые стали
спаривают ручной дуговой сваркой, дуговой сваркой под флюсом и
в защитных газах, электрошлаковой с нарком и газовой сваркой.
Конструктивные элементы подготовки
кромок и размеры сварных швов выбирают в соответствии с ГОСТ 5264–80,
ГОСТ 8713–79, ГОСТ 14771-76, ГОСТ 15164–78, а также в соответствии
с отраслевыми техническими условиями.
Для ручной дуговой сварки применяют
электроды типа Э46А, Э50А, Э60, Э85 и др. (электроды марок УОНИ-13/45,
УОНИ-13/55, УОНИ-13/65, ВИАМ-25, НИАТ-3М и др.), обеспечивающие
достаточную прочность сварного соединения и высокую стойкость
металла шва против образования кристаллизационных трещин.
Для сварки под флюсом применяют флюсы типа АН-348-А и ОСЦ-45 и
проволоки Св-08, Св-08ГА и Св-10Г2. При этом необходимое повышенное
содержание в шве кремния и марганца достигается частично путем
восстановления их из флюса. Этому способствует применение тонкой
проволоки и малых токов, при которых восстановление кремния и
марганца протекает более интенсивно.
Сварка в защитных газах может осуществляться
в аргоне, гелии, углекислом газе, а также в смеси углекислого
газа с аргоном или кислородом. Однако в производстве в основном
нашла применение только сварка в углекислом газе плавящимся электродом.
Технология сварки среднеуглеродистых
сталей в углекислом газе плавящимся электродом, как и сварка их
покрытыми электродами и под флюсом, основана на снижении доли
основного металла в металле шва и обеспечении благоприятной формы
провара. В качестве электродной проволоки применяют проволоки
Св-08ГС, Св-10Г2, Св-12ГС. Св-08Г2С. В производстве сварка в углекислом
газе для изготовления конструкций из среднеуглеродистых сталей
применяется в незначительном объеме.
Благодаря возможности в широких
пределах изменять коэффициент формы металлической ванны и медленному
остыванию металла ЗТВ при электрошлаковой сварке создаются благоприятные
условия для обеспечения высокого качества сварного соединения
при сварке среднеуглеродистых сталей. Однако при сварке металла,
содержащего более 0,3 % углерода, рекомендуется проводить предварительный
и сопутствующий подогрев конструкции (особенно при кольцевых швах)
до температуры 180...200 °С.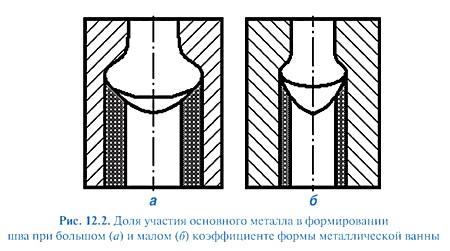
Высокая стойкость металла шва против
кристаллизационных трещин обеспечивается за счет сварки на скоростях
подачи электродной проволоки, не превышающих критические значения.
Следует отметить, что при электрошлаковой
сварке увеличение коэффициента формы металлической ванны при прочих
равных условиях приводит к увеличению содержания в ней углерода
(рис. 12.2).
Увеличение содержания углерода,
сопровождаемое увеличением коэффициента формы металлической ванны,
не приводит к снижению стойкости металла шва против кристаллизационных
трещин, так как одновременно с ростом коэффициента формы металлической
ванны растет критическое содержание углерода.
Серьезной задачей при электрошлаковой сварке сталей с содержанием
более 0,33 % углерода начнется обеспечение равнопрочности металла
шва с основным металлом. Эта задача решается за счет сварочных
проволок Св-10Г2 или Св-12ГС, применяемых при электрошлаковой
сварке. При этом используются флюсы типа АН-8. Достижению требуемых
свойств способствует и переход углерода из основного металла.
Содержание углерода в шве доходит до 0,22–0,24 %. Однако даже
при этом прочностные свойства металла шва находятся на нижнем
уровне свойств основного металла. Для повышения прочности металла
шва рекомендуется применять сварочную проволоку, обеспечивающую
многокомпонентное легирование.
Этот вопрос не нашел еще практического
решения. Высокой ударной вязкости металла шва и участка крупного
зерна ЗТВ для сталей этой группы так же, как и для низкоуглеродистых
сталей, можно достигнуть пока только нормализацией.
Газовую сварку среднеуглеродистых
сталей можно осуществлять проволоками Св-08А, СВ-08ГА, Св-08ГС,
Св-12ГС и др. Качество сварных соединений уступает качеству соединений
при других методах сварки.
|
Низколегированные
стали |
Низколегированными
называются стали, в которых содержание одного легирующего элемента
не превышает 2,0 %, а суммарное содержание легирующих элементов
составляет менее 2,5–4,0 %. К этой группе относятся
низколегированные низкоуглеродистые стали повышенной прочности,
содержащие до 0,23 % углерода и относящиеся к перлитному классу
(14Г, 19Г, 09Г2, 14Г2, 09Г2С, 10ХСНД, 15ХСНД и др.). высокопрочные
низколегированные низкоуглеродистые стали с мартенситной или
бейнитной структурой (14Х2ГМР, 14ХМНДФР и др.) и низколегированные
низкоуглеродистые теплоустойчивые стали (12Х1МФ, 12MX, 15ХМ,
15M, 20ХМ, 15X1М1Ф, 20ХМФ и др.), относящиеся в основном к перлитному
классу.
Технология сварки низколегированных
низкоуглеродистых сталей строится на той же основе, что и технология
сварки низкоуглеродистых сталей, но с учетом особенностей их
сварки. Режимы сварки низколегированных и низкоуглеродистых
сталей различаются незначительно и зависят от конструкции соединения,
типа и техники сварки.
Конструктивные элементы подготовки
кромок под сварку и размеры сварных швов выбирают такими же,
как и при сварке углеродистых сталей.
Низколегированные
стали повышенной прочности обладают хорошей свариваемостью,
а высокопрочные и теплоустойчивые низколегированные стали –
удовлетворительной свариваемостью.
Особенностями сварки низколегированных
низкоуглеродистых сталей повышенной и высокой прочности по сравнению
с нелегированными низкоуглеродистыми являются их большая склонность
к перегреву, росту зерна, образованию закалочных структур, меньшая
стойкость металла шва против кристаллизационных трещин, возможное
разупрочнение, когда свариваются термоупрочненные стали, большая
чувствительность к концентрации напряжений.
При сварке низколегированных сталей
к параметрам режима сварки предъявляются более жесткие требования,
чем при сварке нелегированной низкоуглеродистой стали. Сварка
ограничивается узкими пределами режимов, чтобы одновременно
обеспечить минимальное количество закалочных структур и уменьшить
перегрев. Металл шва для обеспечения равнопрочности с основным
металлом должен обладать более высокой, чем при сварке низкоуглеродистой
стали, прочностью, что достигается в основном за счет легирования
его элементами, переходящими из основного металла. При сварке
металла большой толщины можно использовать подогрев.
Повышение стойкости металла шва
против кристаллизационных трещин достигается путем установления
содержания в металле шва углерода не более 0,15 %, снижения
легирующих элементов (применяется электродная проволока с пониженным
содержанием этих примесей) и обеспечения благоприятной формы
провара (увеличение коэффициента формы провара, уменьшение доли
основного металла в металле шва).
К качеству сварного соединения обычно предъявляются повышенные
требования (отсутствие в швах пор, непроваров, подрезов, плавность
перехода от шва к основному металлу и др.), так как эти стали
чувствительны к концентрации напряжений.
В зависимости от предрасположенности
основного металла к росту зерна и требований к сварному соединению
после сварки назначают термообработку. Для сталей, склонных
к росту зерна, обычно назначают нормализацию, для сталей, не
склонных к росту зерна, как правило, ограничиваются отпуском
при температуре 650 °С.
На практике низколегированные
низкоуглеродистые стали повышенной и высокой прочности чаще
всего сваривают ручной дуговой сваркой, дуговой сваркой под
флюсом и в защитных газах, электрошлаковой сваркой, порошковой
проволокой.
Для ручной дуговой сварки, как
правило, применяют электроды типа Э42А, Э46А, Э50А, Э55 (электроды
марки УОНИ-13/45, СМ-11, УП-1/45, УП-2/45, ОЗС-2, УОНИ-13/55,
ДСК-50,УП-1/55 и др.).
При сварке под флюсом в большинстве
случаев применяют флюсы АН-17, АН-17М, АН-15, АН-22, АН-42,
АН-10, АН-348-А, ОСЦ-45 или АН-60 и проволоки Св-08ГА, Св-10Г2,
Св-08ХМ, Св-08ХМФА, Св-10НМА.
Сварка в защитных газах чаще всего
осуществляется с использованием углекислого газа, а также смесей
углекислого газа с аргоном или кислородом и проволок Св-08Г2С,
Св-12ГС, Св-10ХГ2С.
Применяется сварка порошковыми проволоками ПП-АН8, ПП-АН10,
ПП-АН4, ПП-АН9.
Электрошлаковую сварку в основном
осуществляют с применением флюсов АН-8, АН-22 проволоками Св-08ГС,
Св-10Г2.
Низколегированные низкоуглеродистые
теплоустойчивые стали чувствительны к термическому циклу при
сварке, следствием которого являются появление кристаллизационных
и холодных трещин, процессы старения, разупрочнения, охрупчивания
и опасность локальных трещин при эксплуатации.
Основными
мерами борьбы с этими процессами являются:
-
применение основного металла с минимальным содержанием примесей
и пониженным содержанием углерода;
-
ограничение содержания углерода в металле шва в пределах 0,07–0,12
% и обеспечение необходимых свойств металла шва путем дополнительного
введения легирующих элементов (хрома, молибдена, ванадия,
вольфрама), не вызывающих усиления развития диффузного перераспределения
углерода между основным металлом и металлом шва с образованием
прослоек;
-
обеспечение близкого химического состава основного металла
и металла шва (в первую очередь это относится к содержанию
карбидообразуюшихся элементов, чтобы исключить протекание
диффузионных процессов при эксплуатации);
-
сварка с предварительным или сопутствующим подогревом. Например,
для сталей 12MX, 15XM температура подогрева составляет 200...250
°С, для сталей 20ХМФ, 15X1М1Ф – 350...450 °С (для предотвращения
образования холодных трещим);
-
выбор рационального режима сварки;
-
проведение нагрева и охлаждения с малыми скоростями (30–70
°С/ч) с целью предотвращения развития значительных внутренних
напряжений, так как эти стали обладают пониженной теплопроводностью
и повышенным коэффициентом линейного расширения;
-
термообработка после сварки (высокотемпературный отпуск или
нормализация и высокотемпературный отпуск).
На
практике низколегированные низкоуглеродистые теплоустойчивые стати
чаше всего сваривают ручной дуговой сваркой, дуговой сваркой под
флюсом и в защитных газах.
Ручную дуговую сварку, как правило,
осуществляют электродами с основным покрытием: сварку стали 12MX
– электродами типа Э-09МХ (например, марки ЦУ-2МХ); сварку сталей
12Х1МФ, 15Х1М1Ф, 20ХМФ-Л – электродами типа Э-09Х1МФ (марки ЦЛ-20)
или типа Э-10Х1М1НФБ (марки ЦЛ-36 и др.). Для сварки сталей 12МХ,
15МХ и 20МХ-Л могут также использоваться электроды типа Э-09МХ
(марки ЦЛ-14) с кислым покрытием.
Сварку под флюсом целесообразно вести с использованием следующих
сочетаний: флюса АН-22 с проволокой Св-08ХМФА или флюса АН-17М
с проволокой Св-08ХГСМФА.
При сварке в защитных газах используют
как аргон, так и углекислый газ. Сварку в аргоне часто осуществляют
вольфрамовым электродом (выполнение корневых швов без подкладок).
Присадочную проволоку выбирают близкую по составу к основному
металлу, например для стали 12МХ – проволоку Св-08МХ. Для дуговой
сварки в углекислом газе также используют проволоку, близкую по
составу к основному металлу, но с повышенным содержанием кремния
и марганца, например для стали 20ХМ – проволоку Св-10ХГ2СМА, для
сталей 12Х1МФ, 15Х1М1Ф, 20ХМФ-Л - проволоку Св-08ХГСМФА. |
12.1.4.
Среднелегированные стали |
Среднелегированными
называются стали, в которых содержание одного легирующего элемента
не превышает 2,0–5,0 %, а суммарное содержание легирующих элементов
менее 2,5–10 %. К этой группе относятся среднелегированные стали
перлитного класса типа 20ХГСА, 25ХГСА, 30ХГСА, 35ХГСА, 30ХГСНА
и мартенситного класса типа 30Х2НМФА, 30Х2ГН2СВМА, 33X3НВФМА
и др.
Среднелегированные стали, как
правило, обладают ограниченной свариваемостью.
Характерными трудностями
при сварке этих сталей являются:
-
склонность сварных соединений к холодным трещинам;
-
образование кристаллизационных трещин в металле шва;
-
необходимость получения металла шва, ЗТВ и сварного соединения
в целом с механическими свойствами, равноценными или близкими
к свойствам основного металла.
Опасным
дефектом при сварке среднелегированных сталей являются холодные
трещины. Для предупреждения образования холодных трещин рекомендуется
применять следующие меры:
-
Выбирать для сварных конструкций марки стали, обладающие требуемыми
свойствами при возможно более низком содержании углерода и
легирующих элементов, повышающих восприимчивость стали к закалке
и, соответственно, ограничивать содержание этих элементов
в металле шва.
-
Предъявлять дополнительные требования к основному металлу
в части обеспечения химической и структурной однородности.
Не допускать наличия в стали шлаковых включений неблагоприятной
формы, а также дефектов типа расслоев, которые резко снижают
стойкость сварных соединений против трещин.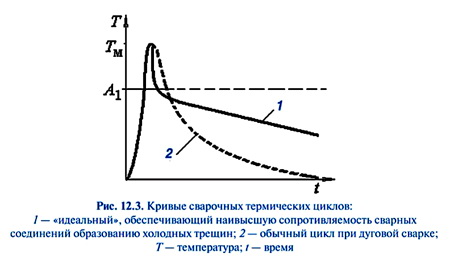
-
Применять методы сварки и сварочные материалы, обеспечивающие
однородность металла шва с основным металлом по химическому
составу и структуре.
-
Уменьшать содержание водорода в основном металле и особенно
в металле шва.
-
Регулировать сварочный термический цикл путем применения оптимальных
режимов сварки. «Идеальный» термический цикл, обеспечивающий
наиболее высокую стойкость сварного соединения против холодных
трещин, приведен на рис. 12.3.
Практическое
осуществление циклов, близких к «идеальному», при дуговой сварке
сопряжено с применением весьма малопроизводительных режимов
сварки, предварительного, сопутствующего и последующего подогрева.
Следовательно, осуществление «идеального» цикла требует больших
затрат труда и средств.
При электрошлаковой сварке этот
«идеальный» цикл неосуществим. В практике термические циклы,
близкие к «идеальным», применяются редко.
6.Подвергать незамедлительной термообработке
соединения после сварки (низкий или высокий отпуск). Это надо
производить в период от момента окончания сварки до момента, пока
холодные трещины еще не возникли. В одних случаях это время составляет
несколько десятков часов, в других – несколько минут.
7. Применять сварку с предварительной
наплавкой кромок. Сущность способа состоит в том, что перед сваркой
на кромки наплавляется слой аустенитного или ферритного металла,
не закаливающегося при сварке шва (создание благоприятного напряженного
состояния на границе раздела металл наплавки – основной металл).
Этот способ применяется редко, так как является трудоемким и дорогим.
В зависимости от структурного
состояния деталей, поступающих на сварку, возможны два основных
варианта: элементы поступают на сварку в термообработанном (закалка
или нормализация с отпуском) состоянии на оптимальные свойства;
термическую обработку, обеспечивающую оптимальные свойства металла,
проводят после выполнения сварочных работ.
В первом случае прочность
сварного соединения определяется прочностью зоны разупрочнения.
Более высокие свойства сварного соединения получают, используя
режимы с малой погонной энергией. Если возможно, выполняют многослойную
сварку. Однако режимы с малой погонной энергией могут привести
к образованию холодных трещин. Образованию холодных трещин при
сварке деталей в термообработанном состоянии способствует также
повышенная жесткость металла. Для предотвращения образования холодных
трещин и уменьшения потерь свойств в зоне разупрочнения при соединении
термообработанных деталей используют режимы сварки, характеризующиеся
малом величиной погонной энергии, в сочетании с предварительным
или сопутствующим локальным подогревом (локальная термообработка)
и отпуском после сварки. Локальную термическую обработку осуществляют
путем последовательного перемещения дополнительного источника
нагрева: газового пламени, плазменной струи, светового луча, индуктора.
Локальная термообработка может быть совмещена со сваркой или выполнена
отдельно.
Если в этом случае не удается предотвратить
образование трещин, используют проволоку, обеспечивающую получение
металла шва с аустенитной структурой. Такой металл обладает высокой
пластичностью и не претерпевает полиморфных превращений, т.е.
сохраняет аустенитную структуру во всем диапазоне температур,
вследствие этого растворимость водорода в шве с понижением температуры
изменяется незначительно, а проницаемость его мала. В этом случае,
как правило, прочность соединении определяется прочностью металла
шва.
Для получения высоких механических
свойств металла шва (на уровне термоупрочненного основного металла)
необходимо при сварке уменьшать объем сварочной ванны и, соответственно,
увеличивать скорость ее кристаллизации и остывания и легировать
металл шва элементами-модификаторами, способствующими измельчению
первичных кристаллитов. Все это делается для измельчения первичной
структуры металла шва.
Если полную термическую обработку
производят после сварки, то основным критерием выбора режима сварки
служит предотвращение образовании холодных трещин. Не следует
применять режимы сварки с заведомо большой погонной энергией,
так как их использование способствует более интенсивному формированию
структур перегрева. По этой причине иногда сварку ведут на режимах
с малой погонной энергией, но в сочетании с подогревом (общим
или локальным). При этом надо, чтобы была идентичность шва и основного
металла по химическому составу. При сварке необходимо предупредить
засорение металла шва серой, фосфором, газами (кислородом, азотом,
водородом) и шлаковыми включениями, а также обеспечить возможно
более мелкозернистую первичную структуру металла шва. Грубозернистая
структура участка перегрева ЗТВ практически полностью ликвидируется
при термообработке.
Для предотвращения образования холодных
трещин в зоне сварных соединений проводят промежуточную термообработку
– общую или локальную.
Для предупреждения образования кристаллизационных
трещин необходимо снижать содержание в металле шва серы, углерода
и других элементов, снижающих стойкость его против кристаллизационных
трещин, а также путем легирования шва такими элементами, как марганец,
хром, и другими элементами, повышающими стойкость металла шва
против кристаллизационных трещин.
Сварку среднелегированных сталей
в производственных условиях чаще всего выполняют ручной дуговой
сваркой, дуговой сваркой под флюсом и в защитных газах, эдектрошлаковой
сваркой, электроннолучевой сваркой.
Конструктивные элементы подготовки
кромок под сварку и размеры сварных швов выбирают такими же, как
и при сварке углеродистых сталей.
В настоящее время ручная
дуговая сварка покрытыми углеродами нашла достаточно широкое применение
для изготовления сварных конструкций из среднелегированных сталей.
К главным особенностям этого способа сварки среднелегированных
сталей следует отнести использование электродов с фтористо-кальциевым
покрытием, широкое применение постоянного тока обратной полярности,
выполнение швов большого сечения каскадным и блочным методами.
Используя эти технологические приемы, стремятся, чтобы разогрев
района шва, особенно при сварке сталей большой толщины, был возможно
более высоким. Существенный эффект в части предупреждения трещин
наблюдается тогда, когда температура разогрева района шва превышает
150 °С. В соответствии с этим длину ступени каскада принимают
обычно равной 100–200 мм.
Ручную дуговую сварку выполняют
электродами, обеспечивающими получение среднелегированного металла
шва типа Э85 (марки УОНИ-13/85), типа Э100 (ВИ 10-6), типа Э125
(НИАТ-3М), типа Э150 (НИАТ-3) и электродами, обеспечивающими получение
аустенитного металла шва типа Э-11Х15Н25М6АГ2 (НИАТ-5).
Сварку под флюсом, как правило, применяют как автоматическую сварку.
Автоматическая сварка под флюсом
рекомендуется при толщине свариваемого металла свыше 4 мм для
прямолинейных и кольцевых (диаметром 80 мм и выше) соединений.
При толщине свариваемого металла менее 4 мм наблюдается коробление
и увеличение числа дефектов в шве. Однако при необходимости под
флюсом сваривают и детали с толщиной кромок 2–3 мм. Сварку под
флюсом можно производить как на переменном, так и на постоянном
токе. Диаметр сварочных проволок 2–5 мм.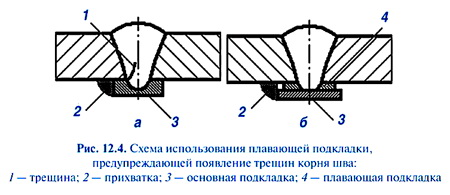
Автоматическую сварку под флюсом
можно выполнять как с разделкой кромок (при больших толщинах деталей),
так и без нее. Для предупреждения прожогов при односторонней сварке
применяют остающиеся (стальные) и съемные подкладки (медные или
в виде флюсовой подушки). При применении медных подкладок мель
может попасть в металл шва, что вызывает образование кристаллизационных
трещин. С целью предупреждения попадания меди и более качественного
формирования проплава иногда применяют флюсо-медную подкладку.
Применение отстающих приваренных стальных подкладок при сварке,
например, замыкающих швов сосудов из стали 30ХГСА, приводит к
образованию трещин 1 в корне шва (рис. 12.4, а) в процессе сварки,
а иногда и при термической обработке (если состав материала подкладки
отличен от состава основного металла изделия). В этом случае целесообразно
применять дополнительную тонкую «плавающую подкладку» 5 толщиной
1,0–1,5 мм, предупреждающую приваривание основной подкладки 3
(рис. 12.4, б).
Подкладные кольца и замковые соединения,
например для сварки стали 30ХГСНА, не рекомендуются, так как они
снижают надежность изделия в эксплуатации.
Вместо подкладных колец первые слои
целесообразно выполнять аргонодуговой сваркой на весу.
Для сварки под флюсом используют флюсы АН-348-А, ОСЦ-45, АН-15,
АН-15М, АН-20, АН-24 и низколегированную или среднелегированную
проволоку, например, Св-18ХМА, Св-10Х16Н25 и др.
Существенное увеличение производительности
сварки под флюсом среднелегированных сталей возможно при ее осуществлении
двумя и более проволоками.
Сопоставление таких
способов сварки двумя проволоками, как однодуговая сварка, двудуговая
сварка, двудуговая сварка на форсированном режиме на второй дуге,
сварка одной дугой на форсированном режиме с подачей дополнительной
подогретой присадочной проволоки, показало, что сварка с подогретой
присадкой наиболее перспективна с точки зрения повышения производительности
с сохранением высокого качества сварных соединений.
Дуговую сварку в защитных газах
можно осуществлять в среде как инертных, так и активных газов.
При этом предпочтение следует отдавать автоматической и полуавтоматической
сваркам, обеспечивающим наилучшее качество швов и высокую производительность
процесса.
В качестве инертных газов используют
чистый аргон и технический гелий; в качестве активного газа используют
сварочный углекислый газ. Сварка может быть осуществлена неплавящимся
(вольфрамовым) и плавящимся электродами. При сварке в активном
газе применяют только плавящийся электрод. В качестве неплавящихся
электродов для ручной и автоматической сварок на постоянном токе
прямой полярности применяют вольфрамовые прутки, лантанированные
вольфрамовые прутки, а также прутки из торированного вольфрама
и итерированного вольфрама; при сварке на переменном токе применяют
чистые вольфрамовые прутки. Активированный вольфрам при постоянном
токе повышает стабильность катодного пятна на конце электрода,
вследствие чего повышается устойчивость дуги в широком диапазоне
рабочих токов.
Проволоку для сварки выбирают в
зависимости от состава свариваемой стали. Например, Св-08ГСМТ,
Св-10ГСМТ, Св-18ХМА, СВ-18ХГСА, Св-08Х20Н9Г7Т и др.
При сварке проволокой Св-18ХМЛ в качестве
защитной среды рекомендуют использовать газовую смесь аргона с
5 % углекислого газа, обеспечивающую при сварке хорошее формирование
сварных швов и незначительное разбрызгивание.
Формирование сварных швов улучшается
при сварке с использованием смеси газов – аргона и гелия (до 25
%); чтобы избежать пористости в шве, а также улучшить устойчивость
горения дуги при сварке на переменном токе, дополнительно вводят
небольшое количество кислорода (до 1 %).
Неплавящимся электродом рекомендуется
сваривать изделия из материала толщиной не более 4–5 мм. Сварку
плавящимся электродом можно применять при изготовлении изделий
толщиной 1 мм и выше. Для материала толщиной до 2 мм рекомендуется
автоматическая аргонодуговая сварка неплавящимся электродом без
присадки или с присадочной проволокой; целесообразна сварка импульсной
дугой. При большей толщине сварку производят с применением присадки.
При сварке сталей толщиной 3–5 мм
высокое качество сварных соединений может обеспечиваться следующим
образом. Первый слой выполняют без присадки с полным проваром
кромок стыка, второй – с поперечными колебаниями электрода и механической
подачей присадочной проволоки. Глубина проплавления при этом должна
быть 60–70 % толщины основного металла. Сварку производят короткой
дугой с дуговым промежутком 0,5–1,0 мм. Указанный метод сварки
применяют для уменьшения перегрева сварного соединения, получения
благоприятной кристаллизации металла шва, уменьшения коробления
и повышения механических свойств сварного соединения. При этом
возрастают пластичность, вязкость шва, сопротивление развитию
трещин и конструктивная прочность сварных соединений; металл шва
не имеет столбчатой направленности; не обнаруживается перегрева
металла в ЗТВ; шов имеет форму с плавными переходами к основному
металлу.
При необходимости сварки на весу
рекомендуется применять аргонодуговую сварку переменным током
промышленной или повышенной частоты (хотя возможно выполнение
сварки и на постоянном токе прямой полярности). Сварку неплавящимся
электродом производят без скоса кромок в один проход для толщин
2,5–4,0 мм на переменном токе промышленной частоты, а для толщин
1,0–2,5 мм на токе повышенной частоты.
Сварку неплавящимся электродом на
постоянном токе рекомендуется производить в два прохода: для толщин
1–3 мм без разделки кромок, свыше 3 мм – с разделкой. При сварке
без разделки кромок первый проход можно осуществлять без присадки,
а при сварке с разделкой – как без присадки, так и с присадкой
(в зависимости от формирования проплава). Если проплав имеет вогнутую
поверхность, то следует применять присадку при сварке как первого,
так и второго слоя. При свободном доступе к шву со стороны проплава
возможна сварка с двух сторон без присадки.
В процессе сварки обратную сторону
сварного соединения шва надо защищать от воздействия воздуха путем
подачи аргона в продольную канавку в подкладке из коррозионно-стойкой
стали. Глубина канавки составляет примерно половину толщины свариваемой
стали, а ширина – четыре – шесть толщин.
Во избежание перегрева сварного
соединения и уменьшения его деформаций применяют импульсно-дуговую
сварку вольфрамовым электродом на постоянном токе прямой полярности.
Для увеличения проплавляющей
способности дуги при аргонодуговой сварке применяют
активирующие флюсы. Применение активирующих флюсов (например,
флюса ФС-71) повышает проплавляющую способность дуги в 1,5–2 раза
(рис. 12.5), что обеспечивает значительный экономический эффект
за счет повышения производительности процесса, повышения качества,
исключения разделки кромок и многопроходной сварки при толщинах
8–10 мм.
Для
получения качественных сварных соединений конструкционных сталей
больших толщин (до 80–100 мм) применяют импульсно-дуговую
сварку плавящимся электродом в щелевом зазоре между кромками.
При этом устанавливают зазор 10–12 мм с помощью соответствующего
притупления кромок. Диаметр проволоки 1,6–2,0 мм. При толщине
металла более 50–60 мм сварку ведут с двух сторон. Зазор заполняют
послойно со скоростью 25–30 м/ч с числом слоев в зависимости от
толщины металла. В качестве защитного газа может быть использован
аргон или смесь аргона с углекислотой. Многослойная сварка в щелевидную
разделку обеспечивает раздробленную структуру металла шва с отсутствием
грубых дендритов и малую протяженность ЗТВ.
Применение электрошлаковой сварки
наиболее рационально для соединения толстолистовых конструкций.
Для электрошлаковой сварки применяют
флюсы типа АН-8, АН-8М, АН-22 и др.
При выборе электродной проволоки
для электрошлаковой сварки следует исходить из требований к составу
металла шва. Флюс практически мало влияет на состав металла шва
вследствие малого его количества, поэтому только в случае необходимости
легирования шва элементами, обладающими большим сродством к кислороду
(например, титан, алюминий), следует применять флюсы на основе
фторидов или системы СаР2 – СаО – Al2O3.
Электродные проволоки при сварке
проволочными электродами и плавящимся мундштуком в зависимости
от состава свариваемой стали и требований, предъявляемых к шву,
выбирают из числа групп легированных или высоколегированных проволок,
например Св-08Г2С, Св-08ГСМТ, Св-18ХМА, Св-10Х5М и др. Пластины
при сварке плавящимся мундштуком и пластинчатыми электродами изготавливают
из аналогичных сталей. Для предупреждения кристаллизационных трещин
в шве необходимо выполнять сварку на режимах, обеспечивающих получение
относительно неглубокой и широкой металлической ванны. Для предупреждения
трещин в околошовной зоне (ОШЗ) при сварке жестко закрепленных
элементов необходимо применять предварительный подогрев до температуры
150...200 °С.
Низкие скорости охлаждения ОШЗ при
электрошлаковой сварке приводят к длительному пребыванию ее в
области высоких температур, вызывающих рост зерна и охрупчивание
металла, поэтому после электрошлаковой сварки среднелегированных
высокопрочных сталей необходима высокотемпературная термообработка
сварных изделий для восстановления механических свойств до необходимого
уровня. Время с момента окончания сварки до проведения термообработки
должно быть регламентировано.
При электронно-лучевой сварке деталей
из среднелегированных сталей обеспечиваются большая глубина проплавления
(до 30–60 мм) и, следовательно, высокая производительность процесса
при изготовлении конструкций из толстолистовых заготовок. Электронно-лучевую
сварку применяют для соединений в труднодоступных местах или в
случае, когда требуется только присущее электронно-лучевой сварке
глубокое и узкое проплавление с минимальными размерами ЗТВ и минимальными
деформациями.
Среднелегированные стати различных
марок при толщине до 25–30 мм можно сваривать электронным лучом
за один проход без предварительного подогрева. Электронно-лучевой
сваркой можно сваривать за один проход стали различной толщины.
Швы, сваренные при большой скорости
с применением высоковольтных источников, в закаленном состоянии
имеют зону разупрочнения 0,2–0,5 мм, что не снижает прочность
сварного соединения. В этом случае мягкая отожженная зона «поддерживается»
более прочным основным металлом и прочной зоной металла шва, из-за
чего разрушение происходит по основному неразупрочненному металлу.
Рекомендуется стыковое соединение
на подкладке из того же материала с последующим удалением ее механическим
способом. Толщина подкладки должна быть не менее 1/5 толщины свариваемого
материала при ширине 15 мм; допускается использование многослойной
подкладки с толщиной каждого слоя 1,5–2,0 мм. Возможна также стыковая
сварка на весу.
Свариваемые кромки необходимо подвергать
механической обработке под углом 90°, заусенцы следует удалять
без скругления кромок.
Необходимо предусматривать припуск
(0,8–1,0 мм) по толщине свариваемых кромок на обработку лицевой
и корневой поверхности шва для ликвидации возможных подрезов и
неравномерных проплавов. Если конструкция сварного соединения
исключает доступ для обработки поверхности корня шва, необходимо
предусмотреть выступ типа остающейся подкладки (при замковом соединении),
который будет предотвращать проплавление шва и разбрызгивание
металла.
При электронно-лучевой сварке толстолистовых
изделий (более 20 мм) из конструкционных сталей при неоптимальных
режимах и технологии сварки наблюдаются дефекты, не встречающиеся
при дуговой сварке: пустоты в корне шва (холодные затворы), полости
большой протяженности в литом металле (паровые мешки) и узкие
щели вдоль оси шва (горячие трещины). Для устранения дефекта в
корне шва рекомендуется уменьшать концентрацию мощности в электронном
пучке, например путем его расфокусировки до определенных пределов
(до 105 Вт/см2). Однако при этом увеличивается ширина и уменьшается
глубина шва, что не всегда желательно. Более эффективно вывести
дефект в корне шва в подкладку с ее последующим удалением. Дефекты
в виде полостей в металле шва устраняют при скорости ниже некоторого
предела.
|
Высоколегированные
стали и сплавы |
К
этой группе металлов относятся легированные стали с содержанием
легирующих элементов более 10 % и сплавы на железоникелевой
и никелевой основах типа ХН35ВТ, ХН35ВТР, ХН35ВТЮ, ХН77ТЮР,
Х20Н80, ХН78Т, ХН67ВМТЮ и др.
В зависимости от свойств высоколегированные
стали и сплавы делят на коррозионно-стойкие, жаропрочные и жаростойкие.
Такое деление условно. Например, сталь Х18Н10Т применяют в качестве
коррозионно-стойкого и жаропрочного материала, а также для изготовления
хладостойкой аппаратуры и т.д. По системе легирования высоколегированные
стали делят на хромистые, хромоникелевые, хромомарганцевые,
хромомарганцеазотистые и т.д.
В зависимости от структуры сталей после охлаждения на воздухе
с высоких температур различают стали ферритные, аустенитные,
мартенситные, аустенитно-ферритные, мартенситно-ферритные, аустенитно-мартенситные
и др.
К сталям мартенситного класса
относятся Х5,Х5ВФ, 2X13, 1Х13Н3, 1Х12Н2ВМФ, 20X13, 15X5, 14X17H2,
11X11Н2В2МФ, 20Х17Н2 и др.
К сталям мартенситно-ферритного класса относятся 1Х11МФ, 15X11МФ,
15Х12ВНМФ, 14X17H2, 12X13, 18Х12ВМБФР, 1Х12В2МФ, 1Х13Н, 2Х12ВМБФР
и др.
К сталям аустенитно-ферритного
класса относятся 08Х22Н6Т, 12Х21Н5Т, 08X21H6M2T, 20X23H13, 08Х18Г8Н2Т,
Х23Н13, Х28АН, 1X21 и др.
К сталям аустенитно-мартенситного
класса относятся X16H6, Х15Н9Ю, Х17Н7Ю, Х15Н8М2Ю, 2Х17Н2 и др.
К сталям аустенитного класса относятся 0Х18Н10, 0Х18Н10Т, Х18Н10Т,
Х14П4НЗТ, Х17НЗМ2Т, 1X14M18, В2ВР, 0Х23Н28, М3Д3Т, 45Х15Г14СЮ
и др.
Основными трудностями при сварке
высоколегированных сталей и сплавов являются: обеспечение стойкости
металла шва и ЗТВ к образованию трещин (горячих и холодных);
обеспечение коррозионной стойкости сварных соединений; получение
и сохранение в процессе эксплуатации требуемых свойств сварного
соединения; получение плотных швов.
Горячим трещинам подвержены в
основном аустенитные стали и сплавы типа X18H10Т, X17HЗM2T,
XH35BT, XH78T и др., холодным трещинам подвержены закаливающиеся
стали мартенситного и мартенситно-ферритного классов типа 2X13,
20Х17Н2 и др.
Кристаллизационные и горячие трещины
при сварке высоколегированных сталей и сплавов могут образовываться
в шве (кристаллизационные трещины) и ОШЗ (горячие трещины).
Высоколегированные стали и сплавы
в большей степени подвержены кристаллизационным трещинам при
сварке, чем углеродистые конструкционные стати.
Это объясняется следующими специфическими
особенностями строения и условий кристаллизации высоколегированных
швов: сильно развитая транскристаллитная направленная первичная
микроструктура; увеличенная литейная усадка кристаллизующегося
металла; значительные растягивающие напряжения, действующие
на сварочную ванну в процессе ее затвердевания; многокомпонентное
легирование, усиливающее вероятность появления малых количеств
легкоплавкой эвтектической составляющей на границах дендритов
в момент завершения кристаллизации сварочной ванны.
Методами борьбы с
кристаллизационными трещинами в высоколегированных швах являются:
создание в металле шва двухфазной структуры (за счет присадочных
материалов); ограничение в нем содержания вредных примесей и
легирование такими элементами, как молибден, марганец, вольфрам;
применение фтористо-кальциевых электродных покрытий и фторидных
сварочных флюсов; применение различных технологических приемов
(увеличение зазора, варьирование коэффициентом формы шва, сварка
тонкой проволокой на умеренных режимах и др.).
Образование в шве двухфазной
структуры (аустенит и первичный феррит, аустенит и первичные
карбиды, аустенит и боридная фаза эвтектического происхождения,
аустенит и хромоникелевая эвтектика) способствует се измельчению.
В результате удастся полностью
или частично подавить транскристаллитную первичную структуру.
Такие швы несравненно более стойки против образования кристаллизационных
трещин, чем однофазные чисто аустенитные.
Предотвращение образования кристаллизационных
трещин в чисто аустенитных швах достигается ограничением содержания
вредных примесей: серы, фосфора, сурьмы, олова, висмута, а также
таких элементов, как кремний, титан, алюминий и ниобий, способствующих
образованию по границам кристаллитов легкоплавких прослоек;
заменой части никеля марганцем; легированием шва молибденом,
вольфрамом, танталом, азотом, рением.
Перечисленные пути предотвращения образования кристаллизационных
трещин в чисто аустенитных швах используют при разработке сварочных
материалов.
Применение фтористо-кальцевых
электродных покрытий и фторидных сварочных флюсов способствует
измельчению структуры металла шва и повышению в результате этого
его стойкости к образованию кристаллизационных трещин, поэтому
при сварке высоколегированных сталей нашли применение электроды
с основным покрытием и фторидные флюсы.
Для повышения стойкости высоколегированных
швов к образованию кристаллизационных трещин можно варьировать
форму шва, увеличение зазора при дуговой сварке тавровых соединений,
использование тонкой проволоки (диаметром 1,2–2 мм) на умеренных
режимах при минимально возможных значениях погонной энергии
сварки, применение сварочных материалов повышенной чистоты,
минимальное проплавление основного металла с целью недопущения
повышения в шве концентрации кремния, меди, серы, фосфора, бора
(речь идет о концентрациях до 0,1 %), могущих вызвать кристаллизационные
трещины.
Горячие трещины появляются в результате
частичного расплавления в ОШЗ по границам зерен или кристаллитов
легкоплавких прослоек эвтектического происхождения и воздействия
на ОШЗ напряжений, возникающих в результате сварочного нагрева.
Таким трещинам особенно подвержены стали и сплавы с повышенным
содержанием серы, фосфора, кремния, марганца в сочетании с медью,
ниобием, легкоплавких примесей олова, сурьмы, свинца, до 0,1
% бора и других элементов, способствующих образованию на границах
зерен легкоплавких прослоек.
Мерами
борьбы с околошовными горячими трещинами являются:
-
создание в ОШЗ двухфазной структуры; применение этого способа
связано с изменением композиции свариваемой стали и поэтому
не всегда возможно;
-
повышение чистоты сталей и сплавов от вредных примесей (серы,
фосфора) и ограничение или исключение в них элементов, инициирующих
образование околошовных горячих трещин (применение электрошлакового
переплава);
-
применение мелкозернистых сталей и сплавов;
-
применение проковки кромок для создания в ОШЗ мелкозернистой
структуры.
При
сварке высоколегированных сталей и сплавов возможно также образование
строчечных, холодных и локальных трещин.
Строчечные трещины образуются
в ЗТВ и обусловлены повышенной загрязненностью сталей и сплавов
неметаллическими включениями и преимущественно строчечным их
залеганием. Трещины этого шва, по-видимому, могут быть как горячими,
так и холодными; они носят они в основном межкристаллический
характер.
Радикальным средством предотвращения
образования строчечных трещин является повышение чистоты сталей
и сплавов в отношении неметаллических включений.
Холодные трещины могут образовываться в шве и ЗТВ при сварке
мартенситных и мартенситно-ферритных сталей, а также малопластичных
сложнолегированных сталей и сплавов. Их образование можно предотвратить
предварительным и сопутствующим подогревом до температур свыше
250...300 °С.
Ряд чисто аустенитных сталей (особенно
легированных ниобием, титаном или с повышенным содержанием углерода)
подвержены так называемым локальным разрушениям.
Локальные разрушения
– это трещины в ЗТВ, возникающие в процессе длительной
эксплуатации изделий при температурах старения сталей (550...700
°С). Одной из причин их возникновения является снижение межзеренной
пластичности аустенитной стали в результате воздействия сварочного
нагрева.
Мерами борьбы с локальными
трещинами являются:
-
снижение содержания углерода в стали до 0,02–0,03 %;
-
исключение из состава стали ниобия;
-
повышение запаса пластичности стали, например с помощью электрошлакового
переплава;
-
применение присадочных материалов, обеспечивающих получение
высокопластичных и менее прочных, чем основной металл, швов.
Обладая
высокой коррозионной стойкостью, аустенитные и хромистые стати
подвержены опасному виду коррозионного разрушения межкристаллитной
коррозии. Межкристаллитная коррозия происходит из-за выпадения
под действием нагрева карбидов хрома (при высоком содержании
хрома в стали) по границам зерен, обеднения границ зерен хромом
и из-за этого пониженной стойкости границ против коррозии. Опасность
межкристаллитной коррозии возникает при нагреве сталей аустенитного
и аустенитно-ферритного классов до температур 300...850 °С,
при нагреве высокохромистых сталей мартенситного, мартенситно-ферритного
и ферритного классов до температур свыше 950 °С. Межкристаллитная
коррозия может возникать в ЗТВ, в шве и на границе «шов – основной
металл» в виде так называемой ножевой коррозии, охватывающей
по ширине всего несколько зерен.
Мерами борьбы с межкристаллитной
коррозией являются:
-
снижение содержания углерода в основном металле и металле
шва до 0,02–0,03 %. При таком малом содержании углерод остается
в твердом растворе при любой температуре и выпадение карбидов
хрома исключается;
-
легирование сталей и швов титаном, ниобием, танталом, цирконием,
ванадием. Обладая большим сродством к углероду, чем хром,
эти элементы дают устойчивые карбиды. В результате карбиды
хрома не образуются и межкристаллитная коррозия исключается;
-
закалка. При нагреве под закалку карбиды хрома растворяются
в аустените, а быстрое остывание фиксирует однородное строение
стали или сплава;
-
стабилизирующий отжиг в течение 2–3 ч при температуре 850...900
°С с охлаждением на воздухе (для хромистых сталей отжиг при
760...780 °С). Это приводит к наиболее полному выпадению карбидов
и стабилизации их состава;
-
получение двухфазной структуры в хромоникелевых сталях (содержание
феррита до 20–25 %) путем дополнительного легирования основного
металла и проволоки хромом, кремнием, алюминием, ванадием,
молибденом, вольфрамом.
Для
предупреждения «ножевой» коррозии применяют также некоторые технологические
приемы, направленные на недопущение или уменьшение
перегрева металла в ОШЗ. К ним относятся: сварка короткой дугой
на максимальных скоростях; сварка очередного валика после полного
остывания предыдущего; сварка слоя, обращенного к агрессивной
среде, в последнюю очередь; охлаждение сварного соединения со
стороны ранее заваренного шва и др.
Общая жидкостная коррозия шва и
ОШЗ возникает в результате воздействия агрессивного реагента на
сварное соединение. Основными методами уменьшения этого вида коррозии
являются сварка изделий швами идентичного с основным металлом
состава и правильный выбор режима термообработки.
Коррозионное растрескивание аустенитной
стали и сварных швов возникает в результате совместного воздействия
растягивающих напряжений и агрессивных реагентов, в частности
хлоридных солей (MgCl2, NaCl), морской воды, бидистиллята, некоторых
кислот.
Меры предупреждения
коррозионного растрескивания: повышение в них содержания
никеля более 40 %; создание двухфазной аустенитно-ферритной или
аустенитно-боридной структуры (содержание бора не менее 0,5–0,8
%); предупреждение коробления и наклепа сварного изделия, способствующих
возникновению растягивающих напряжений в отдельных объемах металла.
При сварке жаростойких сталей и
сплавов для обеспечения жаростойкости сварных соединений следует
стремиться приблизить композицию металла шва к составу основного
металла.
Для обеспечения стойкости металла
шва против образования пор при сварке высоколегированных сталей
необходимо осуществлять удаление влаги из флюсов, электродных
покрытий и газов, со свариваемых кромок и т.д. Флюсы и электроды
следует прокаливать, а газ осушать.
Сварку высоколегированных сталей и сплавов
под фторидными флюсами и электродами с фтористо-кальциевым покрытием
рекомендуется производить на постоянном токе обратной полярности.
При сварке в аргоне некоторых аустенитных
сталей и сплавов рекомендуется к аргону добавлять 2–5 % кислорода.
В остальном требования к высоколегированным
сталям и сплавам в отношении предотвращения пор в швах такие же,
как и при сварке обычных углеродистых сталей.
Получение и сохранение в процессе
эксплуатации заданных свойств сварного соединения при сварке высокохромистых
сталей вызывают значительные трудности. Это связано прежде всего
с охрупчиванием металла в ОШЗ. Охрупчивание связано с укрупнением
зерна в ОШЗ под воздействием сварочного термического цикла.
Для предотвращения охрупчивания металла в ОШЗ рекомендуют высокотемпературный
отпуск при 760...780 °С, значительно повышающий пластичность металла
ОШЗ.
При длительном пребывании при высоких
температурах (500...850 °С) происходит охрупчивание металла. Известны
три вида охрупчивания металла высоколегированных швов: тепловая
хрупкость, сигматизация и старение.
Тепловая хрупкость возникает в результате
нагрева при температурах 350...500 °С высокохромистых (более 15
% хрома) ферритных и аустенитно-ферритных швов, содержащих более
15–20 % сложнолегированного феррита.
Предотвращение тепловой хрупкости можно осуществить ограничением
содержания феррита в двухфазных сварных швах.
Сигматизация
– появление в металле шва при длительной выдержке в интервале
температур 550...875 °С хрупкой структурной составляющей интерметаллида
типа FeCr, известного под названием ?-фазы. Чаше всего ?-фаза
образуется в аустенитно-ферритных и хромистых швах независимо
от их структуры.
Эффективными средствами предотвращения
сигматизации являются нагрев сварных соединений до температуры
1050...1100 °С с последующим быстрым охлаждением, ограничение
содержания первичного феррита (менее 20 %) в двухфазных аустенитно-ферритных
швах, ограничение молибдена, ванадия, вольфрама, хрома, кремния
(элементов, способствующих образованию феррита, который превращается
при указанных условиях в ?-фазу) и повышение концентрации углерода
и азота в чисто аустенитных швах.
Старение происходит
при длительной эксплуатации сварных соединений при температурах
500...750 °С. Оно сопровождается выделением по границам зерен
вторичных карбидов и интерметаллидов в швах и основном металле.
Средством борьбы со старением является
снижение в металле шва содержания углерода и нагрев сварного соединения
до температур выше 900 °С, при которых происходит распад вторичных
карбидов и интерметаллидов.
Для соединения высоколегированных сталей и сплавов применяют следующие
виды сварки плавлением: ручную дуговую сварку, дуговую сварку
под флюсом и в среде защитных газов, плазменную, электрошлаковую
и электронно-лучевую сварку.
Конструктивные элементы подготовки
кромок под сварку и размеры сварных швов выбирают такими же, как
и при сварке углеродистых сталей.
При ручной дуговой сварке высоколегированных
сталей и сплавов преимущественно применяют электроды с фтористо-кальциевым
(основным) покрытием; сварку ведут на постоянном токе обратной
полярности; как правило, сварку осуществляют короткой дугой без
поперечных колебаний конца электрода узким – ниточным – швом с
минимальным проплавлением основного металла; сварку ведут сравнительно
короткими электродами на небольших токах.
Величину тока при сварке в нижнем
положении назначают так, чтобы его отношение к диаметру электрода
не превышало 25–30 А/мм. В проволочном и вертикальном положениях
сварочный ток уменьшают на 10–30 % по сравнению с током, выбранным
для нижнего положения сварки.
В таблице 12.1 приведены наиболее распространенные марки покрытых
электродов для ручной дуговой сварки высоколегированных
сталей.
Сварку под флюсом применяют как
автоматическую сварку и используют для соединения металла толщиной
3–50 мм.
С помощью сварки под флюсом получают
односторонние и двусторонние, однослойные и многослойные швы без
разделки кромок и с разделкой кромок (при толщине металла свыше
12 мм). Возможна сварка с повышенным зазором до 30–40 мм.
|
|
|