|
|
|
|
|
КАРТА
САЙТА
ДОПОЛНИТЕЛЬНАЯ
СПРАВОЧНАЯ
И ПОЛНОТЕКСТОВАЯ ИНФОРМАЦИЯ
ИНФОРМАЦИЯ УЧЕБНОГО
НАЗНАЧЕНИЯ: |
|
|
|
|
|
|
|
|
|
Теодоронский,
В. С. "Озеленение населенных мест с основами градостроительства"
см. здесь....
|
|
|
|
|
|
|
|
|
|
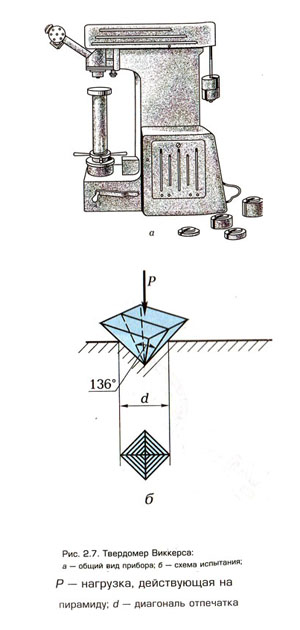 |
|
|
|
|
|
|
|
|
ПОЛНОТЕКСТОВАЯ
ИНФОРМАЦИЯ
УЧЕБНО-ПРАКТИЧЕСКОГО НАЗНАЧЕНИЯ
|
|
|
|
|
Механические
свойства металлов и сплавов // Основы материаловедения (металлообработка)
: учебник для учреждений СПО / ред. В. Н. Заплатин. – 9-е изд.,
стер. – М. : Академия, 2017. – С. 27-37. – (Профессиональное образование.
Металлообработка). |
|
Механические
свойства – это группа свойств, которые характеризуют
способность
конструкционных материалов выдерживать (или не выдерживать)
различные механические нагрузки: прочность, пластичность, упругость,
твердость и ударную вязкость. Под воздействием механических
нагрузок детали машин и механизмы могут разрушаться (или не
разрушаться) в зависимости от механических характеристик.
Для определения механических характеристик
конструкционные материалы подвергают следующим видам механических
испытаний: испытание на растяжение, сжатие, кручение, изгиб,
усталость, динамические испытания (на удар), испытание при повторно-переменных
нагрузках.
Напряжения и виды деформаций, возникающие в деталях машин и
механизмах в процессе их работы.
Напряжение
– это отношение нагрузки к площади поперечного сечения детали,
воспринимающей эту нагрузку (нагрузка измеряется в ньютонах
(Н) или килограмм-силах (кгс), а площадь поперечного сечения
деталей в квадратных метрах (м2)).
Деформация
– это изменение формы и размеров (или разрушение)
деталей под действием нагрузок. В зависимости от направления
действия механических нагрузок различают следующие виды деформации
деталей и механизмов:
-
деформация сжатия, которую испытывают шобот и баба кузнечного
молота, пресса, пуансон и матрица, а также заготовки в процессе
ковки, штамповки и прессования (рис. 2.4, а);
-
деформация растяжения, которую испытывает трос подъемного
крана (рис. 2.4, б);
-
деформация кручения, которую испытывают шпиндель сверлильного
и токарного станков, ходовые винты, валы и др. (рис. 2.4,
в);
-
деформация сдвига или среза, которую можно наблюдать при механической
обработке деталей на металлорежущих станках, зубчатых зацеплениях,
шпонках, шпильках, штифтах, образующих неподвижные соединения
(посадки) деталей и механизмов и т.д. (рис. 2.4, г);
-
деформация изгиба, характерная для стрелы подъемно-мостового
крана, пролетов различных мостов и т.д. (рис. 2.4, д).
|
В
зависимости от физико-механической природы конструкционных материалов
различают упругие и пластические деформации. При упругих деформациях
форма и размеры деталей после снятия нагрузки возвращаются в
исходное состояние. При пластических деформациях происходит
изменение размеров и формы деталей после прекращения нагрузки
(остаточная деформация).
При одинаковых нагрузках и сечениях
детали машин, изготовленные из различных конструкционных материалов,
деформируются по-разному. Например, стальной трос диаметром
10 мм разрушается при нагрузке 5 т, алюминиевая проволока этого
же диаметра разрушается при нагрузке 1 т.
Прочность
конструкционных материалов. Показателем работоспособности
троса (подъема груза) является прочность конструкционного материала.
Прочность
– это способность конструкционных материалов выдерживать
(или не выдерживать) различные механические нагрузки не разрушаясь
(или разрушаясь). Например, трос подъемного крана, изготовленный
из стали, поднимает и перемещает груз определенной массы в пределах
установленной для данной марки стали прочности. Железнодорожный
мост рассчитан на строго заданную грузоподъемность. Прочность
определяется пределом прочности при растяжении (временным сопротивлением),
который характеризует напряжения или деформации, соответствующие
максимальным (до разрушения образца) значениям нагрузки.
Предел прочности
определяется по формуле
|
|
|
|
Пластичность
конструкционных материалов.
Пластичность – это способность конструкционных
материалов изменять свою форму и размеры под действием нагрузки
и сохранять остаточную деформацию после снятия нагрузки. Пластичность
– свойство, обратное упругости. Пластичность характеризуется
относительным удлинением и относительным сужением.
Относительное удлинение
%, показывает, на сколько увеличилась длина образца в процессе
растяжения, и определяется по формуле
|
|
|
|
Относительное
сужение ,
%, показывает, на сколько процентов уменьшится площадь поперечного
сечения образца после растяжения, и определяется по формуле |
|
|
Величина
пластичности зависит от физико-механических свойств конструкционных
материалов, их хрупкости. Хрупкие материалы при растяжении или
других видах деформаций разрушаются без удлинения (изгиба),
внезапно (например, серые чугуны), поэтому хрупкость является
отрицательным свойством материалов.
Свойство пластичности широко используется
в производстве деталей из конструкционных материалов методом
деформирования (прокатки, волочения, ковки, штамповки, слесарных
операций и др.). При этом металл в горячем состоянии деформированию
подвергается значительно легче, чем в холодном состоянии. При
деформировании в холодном состоянии заготовки получают наклеп
(упрочнение). Повышается твердость, прочность, ударная вязкость.
Устраняется хрупкость, уменьшается пластичность. При горячем
деформировании конструкционные материалы повышают механические
свойства: твердость, пластичность, прочность и ударную вязкость;
устраняется хрупкость. При деформировании как в холодном, так
и в горячем состоянии пластическая деформация происходит по
следующим физическим законам:
Эти
важные технологические законы учитываются при выборе технологических
режимов горячего и холодного деформирования.
В практике конструкционные материалы
должны обладать высокой прочностью, некоторой пластичностью. Отсутствие
пластичности приводит к внезапному разрушению деталей. Примеры
пределов прочности, относительного удлинения и сужения некоторых
материалов приведены в табл. 2.2. |
|
|
|
Твердость
конструкционных материалов.
Твердость
– это способность конструкционных материалов противостоять
проникающим нагрузкам. Свойство твердости проявляется при обработке
материалов резанием, в подшипниках качения и скольжения, зубчатых
зацеплениях и различных трущихся деталях и механизмах. Чем выше
твердость деталей и инструмента, тем выше износостойкость и
надежность работы механизмов и стойкость режущих инструментов.
В зависимости от твердости обрабатываемого материала выбираются
режимы обработки заготовок резанием. Твердость режущего инструмента
обусловливает их стойкость (время работы от заточки до заточки).
Конструкционные материалы в сыром состоянии имеют низкую твердость.
Для повышения износостойкости деталей и инструмента их подвергают
различным видам термической или химико-термической обработки,
в процессе которой твердость повышается в 2-3 раза. В металловедении
определение твердости конструкционных материалов основано на
вдавливании в испытуемый образец какого-либо наконечника (индентора)
под нагрузкой. В практике определения твердости металлов широкое
применение нашли методы Бринелля, Роквелла, Виккерса, микротвердости,
упругой отдачи, ударного отпечатка и метод царапания (резания).
Определение
твердости металлов и сплавов по методу Бринелля
проводится на шариковых твердомерах типа ТШ (рис.
2.5). Определение твердости конструкционных материалов в сыром
состоянии (до закалки) по методу Бринелля предусматривает ГОСТ
9012-59*. Твердость по Бринеллю обозначается буквами НВ и числовым
индексом, полученным в результате испытания. Например, 150 НВ.
|
|
Определение
твердости конструкционных материалов вдавливанием в образцы алмазного
конуса (шкалы А и С) или стального закаленного шарика (шкала В)
под определенной нагрузкой (предварительной и основной) называется
методом Роквелла (ГОСТ 9013-59*). Твердость
по методу Роквелла определяется на прибоpax типа TK (с электрическим
приводом) и ТВ (с ручным приводом).
На
рис. 2.6 представлен твердомер типа ТК. Твердость, измеренная
по методу Роквелла, обозначается символами HRC, HRA или HRB (А,
В, С – соответствующие шкалы, зависящие от величины нагрузки)
и цифрами (значения твердости).
Нагрузка
выбирается в зависимости от толщины и условий твердости испытуемых
деталей. Так, стальные закаленные детали толщиной не менее 1 мм
испытываются при предварительной нагрузке 100 Н (10 кгс) и основной
нагрузке 1 400 Н (140 кгс). Общая нагрузка при этом составит 1
500 Н, или 150 кгс. |
|
Методом
Виккерса (ГОСТ 2999-75*) определяют твердость химико-термически
обработанных, а также тонких закаленных деталей путем вдавливания
четырехгранной алмазной пирамиды под нагрузкой 9,807...980 Н (1...100
кгс). Твердость по Виккерсу обозначается буквами HV и определяется
по формуле |
|
|
На
рис. 2.7 приведен твердомер типа ТВ для определения твердости
по методу Виккерса. При измерении твердости по методу Виккерса
основными параметрами являются нагрузка Р = 294,2 Н (30 кгс) и
время выдержки 10... 15 с. |
|
В
этом случае твердость по Виккерсу обозначается индексом HV и числом
твердости (например, 350 HV). При других условиях нагрузка и время
выдержки даются после символа твердости (например, запись 200
HV 10-25 означает, что твердость образца по Виккерсу составляет
200 единиц при нагрузке 100,07 Н (10 кгс) и времени выдержки 25
с.
Числовое значение твердости по Бринеллю
и Виккерсу в пределах 100...450 единиц приблизительно совпадает
с истинной твердостью конструкционных материалов.
В других случаях общего точного
перевода чисел твердости по Виккерсу в числа твердости по ДРУГИМ
методам или в прочность при растяжении не существует.
Выпускаются также универсальные
приборы нового поколения для определения твердости одновременно
по методу Виккерса и Бринелля – приборы мод. 2137ТУ, ХПО-250 и
др.
Ударная вязкость. Способность
конструкционных материалов сопротивляться ударным нагрузкам называется
ударной вязкостью (ударной прочностью). В процессе работы большинство
деталей машин и механизмов испытывают ударные нагрузки, которые
также называются динамическими нагрузками. Для определения условий
работы конструкционных материалов при тех или иных динамических
нагрузках существует метод испытания материалов на ударный изгиб
при различных температурах (ГОСТ 9454-78*). Ударная вязкость (прочность)
определяется на специальном приборе, называемом маятниковым копром
(рис. 2.8). |
Для
определения ударной вязкости материалов изготавливают специальные
образцы с концентраторами напряжений, которые испытывают на маятниковых
копрах. Образцы изготавливают с U-, V-, Т-образными концентраторами.
Образцы устанавливают на опоры маятникового копра посредине концентраторов
напряжений. Далее разрушают образец. В результате разрушения определяют
полную работу К, затраченную на разрушение образца при ударе (работа
удара), или ударную вязкость КС.
Таким образом, под ударной вязкостью
понимают работу удара, отнесенную к начальной площади поперечного
сечения образца в месте концентратора. Ударную вязкость обозначают
KCU, KCV или КСТ в зависимости от вида концентратора (U-образный
концентратор с радиусом 1 мм; V-образный концентратор с радиусом
0,25 мм; Т – трещина усталости, образованная в основании надреза).
Ударная вязкость КС, Дж/м2 (кгс м/см2), вычисляется по формуле
|
|
|
При
определении ударной вязкости, отличной от нормальной температуры,
указывают цифровой индекс, соответствующий температуре испытания.
Например, KCU 20 означает, что испытание проведено при температуре
20°С.
Примеры ударной вязкости некоторых конструкционных материалов
приведены в табл. 2.3.
Испытание
конструкционных материалов на усталость.
Процесс накопления напряжений в деталях и механизмах при знакопеременных
нагрузках, приводящих к разрушению, называется усталостью. Свойство
конструкционных материалов, обратное усталости, называется выносливостью.
В целях определения усталости (выносливости) детали и механизмы
подвергают лабораторным испытаниям, которые регламентируются
ГОСТ 25.502-29. Для определения усталости разработана методика,
по которой испытанию подвергают 15 образцов конструкционного
материала. Каждый образец подвергают нагрузке до полного разрушения
или определенного числа циклов (знакопеременных нагрузок). При
испытании определяют предел выносливости и по соответствующим
параметрам (нагрузкам) определяют гарантийный срок службы (число
циклов), время работы деталей машин и механизмов. В процессе
эксплуатации на эти детали и механизмы даются соответствующие
рекомендации.
|
|
|