|
|
|
КАРТА
САЙТА
|
|
|
|
|
|
Теодоронский,
В. С. "Озеленение населенных мест с основами градостроительства"
см. здесь....
|
|
|
|
|
|
|
|
|
|
|
ПОЛНОТЕКСТОВАЯ
ИНФОРМАЦИЯ
УЧЕБНО-ПРАКТИЧЕСКОГО НАЗНАЧЕНИЯ
|
Устройство
и принцип действия некоторых агрегатов автомобиля // Устройство
автомобилей : учебник для учреждений СПО / Г. И. Гладов,
А. М. Петренко. – 4-е изд., стер. – М. : Академия, 2015. – С.
341-348. – (Профессиональное образование. Автомеханик). |
Двигатель Стирлинга.
Двигатель запатентовал шотландский священник Р. Стерлинг в 1816
г., а реализовал его конструкцию Д. Стирлинг в 1843 г.
При работе двигателя Стирлинга
используется основной закон термодинамики, гласящий, что произведение
объема газа на давление пропорционально произведению газовой
постоянной на температуру, т. е. что газ при нагревании расширяется
и объем его увеличивается, а при охлаждении объем его уменьшается.
Поэтому основным принципом работы двигателя является постоянно
чередуемые процессы нагревания и охлаждения рабочего тела в
закрытом цилиндре. Рабочим телом может служить воздух, водород,
гелий и другие газообразные и жидкие рабочие тела. Цикл двигателя
состоит из четырех фаз, разделенных двумя переходными фазами:
нагрев, расширение, переход к источнику холода, охлаждение,
сжатие и переход к источнику теплоты. Таким образом происходит
расширение и сжатие газа, находящегося в цилиндре, при переходе
от теплого источника к холодному, и наоборот. При этом изменяется
давление, в результате чего можно получить полезную работу (рис.
П1).
Фаза 1. Внешний
источник теплоты нагревает газ в левой части теплообменного
цилиндра. Создается давление, толкающее поршень вправо (вытеснительный
поршень неплотно прилегает к стенкам цилиндра).
Фаза 2.
Маховик толкает вытеснительный поршень влево, тем самым перемещая
разогретый газ из левой части в охлаждающую камеру.
Фаза 3.
Газ охлаждается и сжимается, поршень перемещается влево.
Фаза 4.
Вытеснительный поршень перемещается вправо, тем самым перемещая
охлажденный газ в левую часть цилиндра. Цикл повторяется.
В
машине Стерлинга движение рабочего поршня сдвинуто на 90° относительно
движения поршня вытеснителя. В зависимости от знака сдвига машина
может быть двигателем или тепловым насосом. При нулевом сдвиге
работа не производится.
Наряду с большими преимуществами
двигателя – большой ресурс, высокая экономичность, бесшумность,
обусловленная отсутствием выхлопа, и экологичность, – двигатель
имеет и недостатки. К недостаткам относятся большая материалоемкость,
необходимость работать при высоких давлениях и при высокой теплонапряженности
материалов корпуса двигателя, сложность при создании требуемого
теплообмена и др.
Бесступенчатая
клиноременная передача (вариатор). Бесступенчатые
трансмиссии, как правило, классифицируются по типу передачи,
обеспечивающей бесступенчатое изменение коэффициента передачи.
Вариатор – механическая передача, основанная на передаче вращения
(крутящего момента) трением через промежуточное тело (ремень,
цепь, ролик), которое
можно переводить в любую точку переменного радиуса ведущего
или ведомого шкива, получая необходимое передаточное число.
Наибольшее распространение получил клиноременной вариатор.
Бесступенчатая трансмиссия обеспечивает
постоянную работу двигателя при различных крутящих моментах,
а следовательно – оптимальную динамику разгона и требуемый момент
в зависимости от характеристики дороги. Вариатор не разрывает
потока мощности, тем самым минимизируя расход топлива (рис.
П2).
Главной серьезной проблемой трансмиссии
с клиноременной передачей был ограниченный ресурс клиновидного
ремня (например, передача «Вариоматик»).
Вопрос
практичности вариатора был решен братьями Ван Дорны, запатентовавшими
ремень из наборных пластин. Многослойная конструкция оказалась
существенно выносливей, ремень не тянул муфту, а толкал, благодаря
чему ресурс вариатора значительно увеличивался.
Дальнейшие работы по увеличению
ресурса ремней позволили применить вместо ремня цепь («Ауди»).
Однако, решив задачу прочности передаточного звена, возник вопрос
термоустойчивости. Вариатор сильно нагревался. Решение было
найдено компаниями «Ауди» и ZF, создавшими систему «Мультитроник».
По способу передачи крутящего момента «Мультитроник» относится
к клиноременным вариаторам.
Дальнейшее развитие бесступенчатых
передач позволило создать тороидный вариатор, принцип работы
которого исключает промежуточное звено в виде ремня или цепи.
Момент передается роликами, расположенными на соосных дисках.
Передаточное число такой трансмиссии меняется путем изменения
радиуса, по которому контактируют обоймы с роликами. Грубо говоря,
скорость автомобиля, оснащенного тороидным вариатором, зависит
от взаимоположения контактных роликов. Такой механизм используется
на автомобиле «Ниссан Седрик». Изменить передаточное число вариатора
в данном случае помогает гидравлика: по сигналу электронного
блока управления она сдвигает роликовые обоймы по вертикали.
Нарушенная в результате этого соосность дисков обеспечивает
самостоятельный поворот роликов. Ресурс вариатора – порядка
100 тыс. км пробега.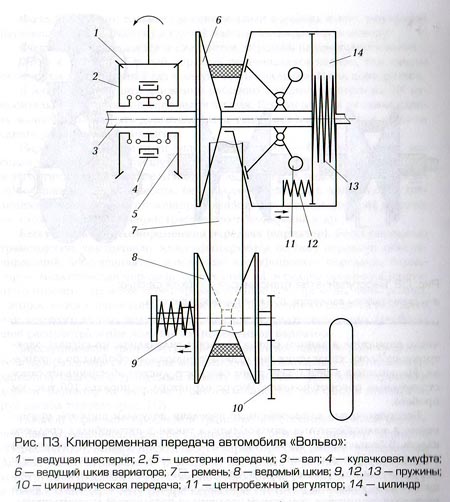
Бесступенчатые клиноременные передачи
получили широкое применение в малогабаритных автомобилях, а
также в автомобилях среднего класса. В большинстве случаев один
или оба шкива (ведущий и ведомый) оборудованы раздвижными боковинам.
Зазор между боковинами шкивов определяется центробежным регулятором.
При повышении частоты вращения вала двигателя и, соответственно,
ведущего вала боковины ведущего вала сдвигаются, тем самым увеличивая
посадочный диаметр шкива, а коэффициент передачи уменьшается.
Клиноременной вариатор на автомобиле
«Вольво» устанавливается в трансмиссии между главной передачей
и ведущими колесами (рис. П3). Изменение передаточного числа
в вариаторе происходит автоматически путем изменения диаметров
шкивов. На поперечных валах закреплены ведущие шкивы вариатора.
Один шкив закреплен жестко, другой может перемещаться вдоль
оси вала. Подвижный шкив связан с грузиками центробежного регулятора
11 и поршнем цилиндра, связанного с впускным трубопроводом двигателя.
Ведомый шкив 8 состоит из подвижного (левого), на который воздействует
пружина 9, и неподвижного (правого) шкивов. Ведомый вал вариатора
через цилиндрическую передачу 10 связан с ведущими колесами
автомобиля. Работает вариатор следующим образом. При трогании
с места (малая частота вращения коленчатого вала) ремень на
ведомом шкиве пружиной 9 выжимается на больший диаметр шкива.
Вследствие малой частоты вращения коленчатого вала грузики регулятора
11 сдвинуты и подвижный шкив под действием пружины 12 смещен
относительно неподвижного шкива – ремень располагается на малом
радиусе (наибольшее передаточное число). По мере разгона автомобиля
увеличивается частота вращения вала 3 и сила действия центробежного
регулятора, который смещает подвижную часть шкива и перемещает
ремень на больший диаметр. С подвижной частью шкива также связан
цилиндр 14, на который воздействует разрежение во впускном трубоприводе.
При уменьшении нагрузки (разрежение во впускном трубоприводе
возрастает) положение ведущего шкива изменяется, перемещая ремень
на больший диаметр и уменьшая передаточное число. Таким образом
происходит автоматическое изменение передаточного числа вариатора
в зависимости от скорости движения автомобиля и нагрузки на
двигатель. По аналогичной схеме работают и другие клиноременные
вариаторы автомобилей.
Резинокордные пневматические
упругие элементы. Пневматический упругий элемент
является основным устройством подвески, обеспечивающим упругую
связь кузова с колесом. Упругим рабочим телом элемента служит
воздух, заключенный в герметичную деформируемую оболочку. Герметичная
оболочка представляет собой прочный многослойный баллон из эластомера
или резинокордного материала, состоящего из нескольких слоев
резинокордной ткани с внешним и внутренним слоями маслостойкой
резины.
По конструкции резинокордные элементы
делятся на баллонные и диафрагменные (рис. П4). Баллонные элементы
могут быть одно-, двух- или трехсекционными, деформирующимися
при колебаниях кузова подобно мехам гармошки. Диафрагменные
упругие элементы отличаются от баллонных наличием поршня, входящего
при деформации упругого элемента внутрь объема, ограниченного
эластичной оболочкой. Воздух в баллонных упругих элементах находится
под давлением 0,5...0,8 МПа, а в диафрагменных давление может
достигать 2,0...2,5 МПа.
Заполнение воздухом резинокордных
упругих элементов осуществляется либо от специального компрессора
на легковых автомобилях, либо от компрессора тормозной системы
на грузовых автомобилях. Наличие компрессора позволяет регулировать
давление в пневмобаллоне в широких пределах, т. е. позволяет
управлять автоматически положением кузова относительно дороги
или изменять жесткость упругого элемента в зависимости от изменения
нагрузки.
Пневматический упругий элемент
состоит из корпуса с направляющей, уплотнительной манжеты и
поршня (в диафрагменном упругом элементе). Конструктивно пневматический
упругий элемент может изготавливаться со встроенным амортизатором
или устанавливаемым отдельно. Упругий элемент, объединенный
с амортизатором, имеет название пневматическая стойка.
В настоящее время пневматическая
подвеска устанавливается на не которых моделях автомобилей бизнес-класса
и больших внедорожниках (например, «Фольксваген Туарег», «Ауди»
Q7 и др.).
Основными достоинствами пневматической
подвески являются комфортабельность, геометрическая проходимость
и безопасность автомобиля.
В ряде случаев пневматическая
подвеска применяется в комбинации с автоматически регулируемыми
амортизаторами. Такая конструкция получила название
адаптивная пневмоподвеска.
Адаптивная пневмоподвеска
имеет следующие устройства:
-
пневматические упругие элементы на каждое колесо;
-
модуль подачи воздуха;
-
ресивер;
-
регулируемые амортизаторы;
-
электронный блок управления.
Система
управления обеспечивает электронное регулирование степени демпфирования
амортизаторов. Она включает в себя входные датчики, блок управления
и исполнительные устройства.
В работе системы
управления подвески используются следующие входные датчики:
-
клавиша настройки демпфирования;
-
датчики дорожного просвета;
-
датчики ускорения кузова.
С
помощью клавиши на панели приборов производится выбор режимов
адаптивной подвески. Датчик дорожного просвета фиксирует величину
хода подвески на сжатие и на отбой. Датчик ускорения кузова
определяет ускорение кузова автомобиля в вертикальной плоскости.
Сигналы от датчиков поступают в электронный блок управления,
где в соответствии с заложенной программой происходит их обработка
и формирование управляющих воздействий на исполнительные устройства
– регулировочные клапаны амортизаторов. При помощи электромагнитных
регулировочных клапанов проходное сечение перетекающей через
клапан жидкости изменяется в зависимости от величины воздействующего
тока. Чем больше ток, тем меньше проходное сечение клапана и,
соответственно, выше степень демпфирования амортизатора («жесткая»
подвеска). Чем меньше ток, тем больше проходное сечение клапана
и ниже степень демпфирования («мягкая» подвеска). Регулировочный
клапан устанавливается на каждый амортизатор. Конструктивно
он может располагаться внутри или снаружи амортизатора.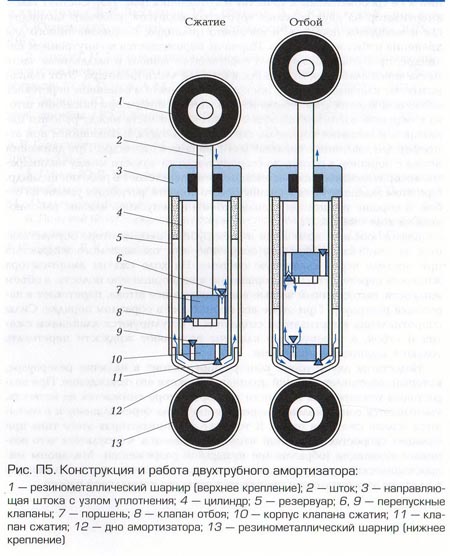
Двухтрубный амортизатор.
В современных подвесках наряду с упругим элементом используют
демпфирующий элемент – амортизатор, поглощающий большую часть
энергии колебаний автомобиля и обеспечивающий необходимый контакт
колеса с дорогой.
Для выполнения своей функции амортизатор
должен поглощать определенное количество энергии колебаний,
практически преобразуя ее в тепловую энергию. Количество поглощаемой
энергии зависит от массы автомобиля, жесткости упругого элемента
в подвеске и частоты колебаний.
Работа гидравлического и гидропневматического
амортизаторов основывается на двух основных свойствах жидкости:
ее несжимаемости и вязкости.
Все производимые в мире амортизаторы
делятся на две группы: гидравлические (или масляные) и гидропневматические
(или газонаполненные).
Принцип работы гидравлического
амортизатора достаточно прост. В рабочем цилиндре, заполненном
специальной гидравлической жидкостью, перемещается шток с поршнем,
имеющим калиброванную систему клапанов. При движении поршня
через калиброванные отверстия клапанов перетекает жидкость,
создавая сопротивление движению поршня, т.е. происходит поглощение
энергии колебаний кузова. Таким образом происходит гашение (демпфирование)
колебаний в подвеске каждого автомобиля.
Гидравлические
двухтрубные амортизаторы – самый распространенный и дешевый
тип демпфирующих устройств. Они просты по конструкции и не требовательны
к качеству изготовления (рис. П5). Состоит такой амортизатор
из двух соосных трубчатых корпусов: рабочего цилиндра, где и
находится поршень, и внешнего цилиндра, предназначенного для
хранения избыточного масла. Поршень перемещается во внутреннем
цилиндре, пропуская масло через собственные каналы и выдавливая
часть масла через клапан, находящийся в нижней части цилиндра.
Этот клапан называют клапаном сжатия, поскольку через него в
основном перетекает масло при ходе сжатия. Масло из рабочего
цилиндра при движении штока с поршнем вытесняется объемом штока
в полость между рабочим цилиндром и внешним корпусом, где сжимает
воздух, находящийся при атмосферном давлении в верхней части
внешнего цилиндра. При движении штока с поршнем в обратную сторону
масло из полости между цилиндрами, которая называется компенсационной,
перетекает в рабочий цилиндр. При этом задействуются клапаны
самого поршня, регулируя усилие на отбой. В поршне установлен
клапан отбоя и перепускной клапан, работающий на ходе сжатия.
Демпфирование колебаний в двухтрубном
амортизаторе осуществляется за счет гидравлического сопротивления,
оказываемого жидкостью при проходе через клапанную систему.
На ходе сжатия амортизатора жидкость перетекает из подпоршневой
в надпоршневую полость, а объем жидкости, вытесненный частью
вошедшего в нее штока, перетекает в наружный резервуар. При
отбое все происходит в обратном порядке. Силы сопротивления
амортизатора создаются и регулируются клапанами сжатия и отбоя,
а перепускные клапаны позволяют жидкости перетекать только в
заданном направлении.
Недостаток двухтрубной конструкции
состоит в наличии резервуара, который охватывает рабочий цилиндр,
усложняя его охлаждение. При возрастании температуры жидкости
в амортизаторе снижается ее вязкость, уменьшается сопротивление
перетеканию масла через клапаны и изменяются усилия сжатия и
отбоя. К тому же в амортизаторах этого типа при больших скоростях
колебаний масло вспенивается, в результате чего возникает кавитация
(образование пузырьков разрежения). Миллионы микроскопических
пузырьков, сливаясь вместе, образуют пену, попадающую в клапаны
амортизатора и препятствующую его нормальной работе.
|
|